Let’s describe a common scenario for workers handling inbound receiving on behalf of buildings, stores, universities, warehouses, etc.
A carrier, like UPS, arrives at the facility, drops off the package, and leaves it in a holding pattern, waiting for personnel to input critical data from the label needed for subsequent workflows. For a residential building or office space, this might mean utilizing that data to notify delivery recipients. For a warehouse, inbound receiving is the first step in capturing inventory, asset management, and fulfillment data.Â
Despite its importance, this process isn’t usually beautiful, modern, or streamlined. After talking with hundreds of professionals in building and logistics operations, we found that the most common ways to record data from shipping labels include pen and paper, spreadsheets, and traditional barcode scanning.Â
So here’s where we are: the package arrives via a carrier, sits in a building’s mailroom or a warehouse’s staging area, and a worker documents data from the shipping label via commonly used manual methods.Â
These methods are likely disconnected from critical tech stack components, slow, and limited in data capture capabilities. Also worth mentioning: these inefficient solutions leave your workforce feeling frustrated and prone to mistakes. So why are logistics teams still stuck with these outdated methods in a world with sophisticated AI models that let you do this with your smartphone?Â
There’s a better way. Optical Character Recognition (OCR) is a technology that transforms images of text into machine-readable text. At PackageX, we utilize intelligent character recognition, enabling cameras to interpret text like humans, relieving workers responsible for manually documenting data from shipping labels.
Here’s how:
Ready to get started and follow along? Check out our API and Vision SDK Documentation. Â
Shipping Labels: What Are They and What’s On Them?Â
A shipping label acts like an ID for your package, providing crucial information about where it is going and helping to guide it to the correct destination. In order to know how to read a shipping label, you should be aware of the critical components of a shipping label:Â
Addresses
- Recipient Information and Address: This includes the complete name of the person or the company receiving the package and their associated street number, city or province, state, and country.Â
- Sender Information and Address (Sometimes): Including a sender’s address is not always necessary but essential for shipping items that might result in returns.Â
‍Tracking and Identification
- Tracking Number: A unique code consisting of numbers and letters assigned to the package by the carrier.Â
- Barcode:Â This representation of the tracking code is usually machine-readable and presented in a linear or QR-code-type format.Â
Shipping Details
- Carrier Information The shipping carrier’s logo is usually displayed on the shipping label for quick identification.
- Shipping Method: A representation of the chosen delivery service (express, overnight, standard), which determines the speed and cost of delivery. Â
- Shipping Weight: Helps handlers process and price the shipment.Â
- Special Instructions: Often, labels indicating noteworthy details about the shipment will be included (e.g., fragile, live animals, perishable)Â
Logistics FieldsÂ
- Purchase Order (PO) Number: A unique identifying number assigned to a purchase order that documents a customer’s intention to purchase the item.Â
- Reference (Ref) Number: A unique identifier a shipper assigns to a shipment to help track its contents through the shipping process.Â
- Return Merchandise Authorization (RMA) number: Unique identifiers assigned to products during a return.Â
- Invoice (INV) number: A unique number that a store uses for billing purposes.Â
Challenges When Scanning Labels
Here are some common challenges you might face when scanning barcodes in shipping and receiving:
Damaged Barcodes: Barcodes can get smudged or scratched during transit, making it difficult for standard scanners to read them. PackageX shipping label scanner extracts information from the entire shipping label, even if the barcode is damaged or unreadable
Slow Processing: Relying on basic barcode scanners can slow down operations, especially during high-volume periods. Many scanners struggle to scan multiple labels at once, resulting in delays and inefficiencies during busy seasons. Our shipping label scanner app greatly accelerates the scanning process. Cloud models deliver results in 2-3 seconds on average, while on-device models process in under 200 milliseconds, offering significantly faster performance than traditional barcode scanners.
Limited Barcode Support: Some scanners are only equipped to handle basic linear or 2D barcodes. PackageX's scanning technology goes beyond standard linear and 2D barcodes, handling a variety of formats like QR codes and logistics-specific barcodes used by FedEx and DHL. It can even digitize handwritten text to cater to different logistics documents and label types.
Benefits of A Smart Label ScannerÂ
- Cost savings: Companies can use budget smartphones instead of expensive scanners, and employees can simply install the already existing company app.
- Portability: Smartphones are lightweight, easy to carry, and can be worn hands-free.Â
- Ease of integration: Smartphones running iOS or Android can easily connect with backend systems, and integrating an SDK into mobile apps takes very little time.
- Versatility & accuracy: Smartphones handle multiple tasks like barcode scanning, track outbound packages, and checking in packages, with software like the PackageX SDK offering high accuracy and ongoing improvements.Â
Steps to Scan a Shipping Label With Your SmartPhone
Scanning a shipping label can happen in seconds but, behind the scenes, many things are happening to ensure data is captured and connected accurately.
Integrating the Vision SDKÂ
With the PacakgeX Vision SDK, you can instantly extract and parse data from paper-based logistics documents, including shipping labels. The first step in processing images with OCR is downloading the SDK, which acts like an engine for images taken with a smartphone’s camera.Â
The SDK integrates with your camera’s interface to control predetermined image capture characteristics. Many PackageX customers choose to improve image capture and processing by controlling for auto-capture, border detection, audio feedback, and more, which can guide the user in capturing high-quality images.
The PackageX SDK combines OCR, Shipping Barcode, and QR code scanning into one tool, accelerating data capture for shipping labels and seamlessly integrating with the OCR API algorithm, which helps make sense of the raw text extracted via the Vision SDK. First, the Vision SDK handles all the difficult development work, like image adjustments, resizing, rotation, and pre-processing. It acts like a bridge for the OCR engine, which performs the core text recognition and data extraction.Â
Capturing the Label Image and Pre-Processing
After the shipping label is captured, there are a few pre-processing adjustments that the Vision SDK might perform to ensure a smooth “handoff” to the OCR algorithm:Â
- Scaling/Cropping: Adjusting the image size or cropping specific regions of interest containing text.
- Brightness/Contrast Adjustment: This enhances image clarity for better character recognition. It is helpful for images captured with poor or dim lighting.Â
- Rotation: The Vision SDK will automatically rotate images captured at abnormal angles.Â
Text Recognition and Sending the Image to the APIÂ
Once the vision scanner captures the image, it turns it into raw text or binary data. The software does this by classifying areas of the image; light areas are classified as background and dark areas as text. OCR technology processes the text from an image by using two distinct strategies:Â
- Feature extraction - Feature extraction defines characters by evaluating their lines and strokes. Based on the evaluation, it searches for the best match. This method is typically used when analyzing handwritten text.Â
- Pattern matching - Pattern matching works by evaluating the whole character, isolating it into an entity called a glymph, and comparing it with glyphs that have already been stored. This method works best with images scanned from documents already well known, like typed text in a predefined font.
Receiving and Processing the Extracted Data
OCR data extraction can be viewed as a series of inferences a system makes about an image's content. An inference is a logical conclusion or deduction made based on processed data. In simpler terms, it's how a system uses artificial intelligence to analyze text from images and video feeds, which allows us to extract and understand the key information.
Inferences are made based on models or learned representations of the OCR system. Models are compromised of rules and equations derived from historical data. At PackageX, we use these machine-learning models to process logistic documents. We can accurately extract and understand important information by training our models on large amounts of data. This is partially achieved via matching or the comparison of extracted features to a database of known character patterns. With matching, we can quickly figure out things, like the courier type and delivery speed, thanks to the patterns and lessons learned from past data.Â
Inferences derived from our Shipping Label model allow us to extract these properties:Â
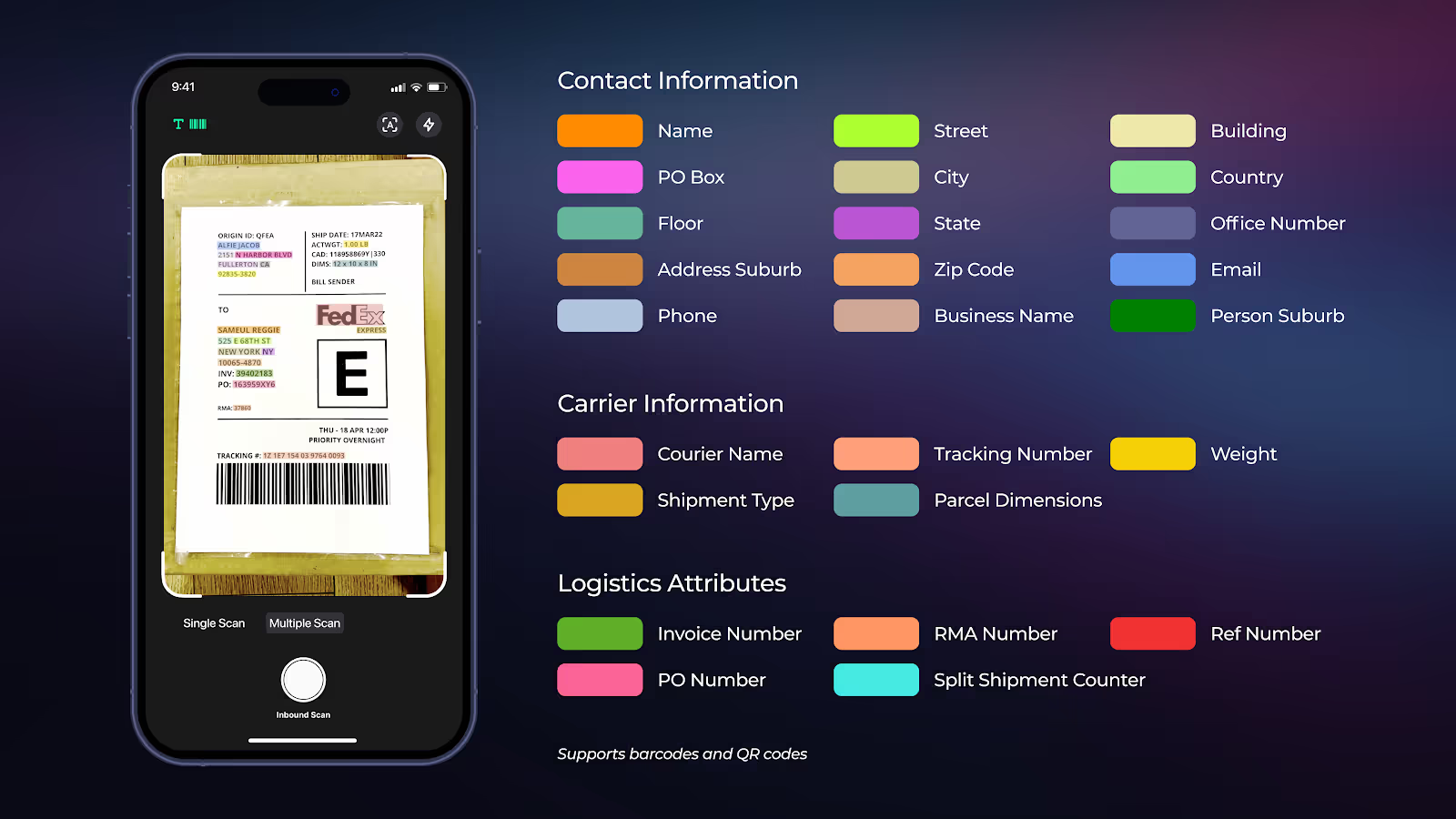
Post-ProcessingÂ
The post-processing phase is crucial for OCR because, during this phase, the raw, extracted data is refined into a structured, accurate, and usable format. This standardization is crucial for ensuring the data can be shared and integrated with other systems such as your WMS, IMS, ERP, etc. This process includes 4 crucial steps:Â
- Data Validation: This step verifies extracted data against predefined formats and rules. It also checks for inconsistencies, typos, or any other missing information.Â
- Data Normalization: This step helps convert data into a standardized format and checks for variations in data, such as address formats and data formats.Â
- Data Enrichment: During the enrichment phase, additional information will be added to the extracted data using APIs. This will include geocoding, carrier information, distance calculation, and more.Â
- Data Structure: During this stage, the organized and finalized data is converted into a structured format (JSON, XML, CSV, etc).Â
{{returns-webinar}}
Sharing Data with Other Systems
Now that the data has been validated, normalized, enriched, and structured, it can be shared with existing systems in your supply chain, such as your WMS, IMS, ERP, and more. By exchanging the data in real-time, businesses can add automation to existing processes, improve accuracy, and gain insights. At PackageX, we help initiate that exchange in two ways:
Webhooks: A lightweight method of real-time data exchange initiated by an event. When a specific action occurs (i.e. a shipping label is effectively scanned), a webhook sends a notification to a predefined URL containing relevant data.Â
Here’s an example of data exchange between the PackageX OCR and a WMS via a webhook:Â
- A shipping label is uploaded via OCR software.Â
- The software extracts and processes relevant data.Â
- Upon successful processing, the OCR sends a webhook notification to a predefined URL associated with the WMS, including extracted data about the label.Â
- The WMS receives the webhook and processes the incoming data.Â
- Based on the data, the WMS can perform actions such as:Â some text
- Creating or updating inventory ordersÂ
- Generating purchase ordersÂ
- Initiating fulfillment processesÂ
- Notifications to relevant warehouse staffÂ
APIs: A programmatic interface for interacting with a system or application via two-way communication. APIs typically use HTTPS requests to perform actions and return structured data formats like JSON. While webhooks are triggered by events, APIs are triggered by requests.Â
Shipping Label Scanning and Use CasesÂ
Is shipping label scanning right for your company? At PackageX, our customers span a variety of industries and use cases but those who utilize our OCR for shipping labels typically process high-volumes of packages and have a need for quick and accurate data extraction from shipping labels. The use cases include but are not limited to:Â
- Inbound Receiving at a Warehouse: As packages come into a warehouse, our Shipping Label OCR serves as the first step in automating inventory receiving, goods verification, and fulfillment.Â
- Efficient Mailroom Operations: For campus mailrooms, residential buildings, or corporate offices that need to scan packages and automate the ingestion of package data to notify recipients of deliveries.
- Returns Processing: For facilities that process returns, our Shipping Label OCR will automate data extraction and populate existing systems used for returns.Â
Are you interested in trying our OCR API to see if it is right for your team? After scheduling a demo, a Sales Engineer will contact you to discuss your unique needs, current tech stack, and more.Â
FAQs
Scanning is one thing, but can I use PackageX to create a shipping label?
Yes! PackageX enables users to connect their shipping accounts to our platform via API key. Get access to preferred and negotiated rates from dozens of carriers including UPS and FedEx with shipping aggregator EasyPost, or use our direct carrier integrations to get rates from providers like DoorDash, USPS, and Frayt.
Once you’ve connected your accounts, use PackageX Shipments to create a label and print it out. Enter sender, recipient, and package details to instantly get rates from every provider who can perform the shipment. Track your package's journey with our interactive tracking map and customize notifications to get package updates through the last mile.
How do you scan a code on a package?
To scan a shipping label with the PackageX app, open the app and tap the shutter icon. Ensure you're in the right mode (inbound or outbound) and align the label within the scan window. The app will automatically scan or you can manually trigger it with the shutter button.