Efficient product handling is essential for businesses to stay competitive in a fast-paced logistics world. One process that has evolved significantly over time is palletizing, the method of arranging items onto pallets for transportation. What used to be a manual, labor-intensive task has been revolutionized by automated palletizing systems that offer greater speed, accuracy, and safety.
Let’s explore what palletizing is and how modern automation technology is transforming the process. Whether you’re handling uniform products or dealing with diverse shapes and sizes, understanding palletizing is important to enhance productivity and cut costs.
What Is Palletizing?
Palletizing is the organized stacking of multiple identical items onto a pallet for shipping purposes. The arrangement is carefully planned based on the weight of the items and follows a pattern designed. This enhances storage density, maintains the integrity of the products, and increases the speed of transport. Fully optimizing the process involves numerous considerations and techniques.
Why Is Palletization Important?Â
Pallets enable the efficient handling of oversized, heavy, or various types of loads using forklifts or pallet trucks. This way, a single worker can manage tasks that would otherwise require multiple people in a shorter time frame. Let’s look at the benefits in detail:
- Improved product stability: Palletizing consolidates multiple products into one stable unit, wrapped with plastic film and stacked in a weight-balanced pattern to prevent shifting or damage. Proper palletization minimizes handling errors and exposure to damage. Standardized pallet sizes facilitate easy use with forklifts and automated machinery, while the strength of pallets supports heavier products.
- Faster product handling and shipment: Pallets enable quicker loading, unloading, and product handling, resulting in faster shipment turnaround and increased transport efficiency.
- Portability and transport efficiency: Pallets are easier to handle and stack across various transportation modes (trucks, ships, planes), simplifying tracking and reducing the number of individual items.
- Better operator safety: Automated and mechanical palletizing reduces the need for repetitive lifting of heavy loads, lowering the risk of injuries to workers.
- Optimized storage utilization: Pallets with standardized dimensions allow efficient stacking and storage, optimizing warehouse space and transportation capacity.
- Improved inventory control: Palletized products allow easier tracking of stock levels, as each pallet represents a known volume of merchandise, enabling better SKU management and monitoring.
So, how can palletizing streamline the movement of goods? Let’s understand the process so we can find solutions to optimize its performance.  Â
Understanding the Palletization ProcessÂ
As we have understood, palletization arranges goods on a pallet to secure and consolidate their load, making it easier to handle and transport. Here’s the step-by-step palletization process:Â
- Maximize box capacity: First, fill boxes to their maximum capacity while considering weight and volume limits. Wrap individual products for extra protection and fill empty spaces to reinforce boxes and prevent crushing during transport.
- Choose the right pallet types: Choose pallets compatible with the automated palletizer system, considering materials (plastic or wood), shapes, dimensions, and weights. Consistency in pallet selection improves efficiency.
- Stack properly: Stack boxes evenly to distribute weight and make sure they don’t shift or topple. Boxes must stay inside the pallet edges to avoid damage.
- Secure with wrap: After loading the pallet, secure it with multiple layers of plastic wrap. If needed, add corner protectors for increased stability.
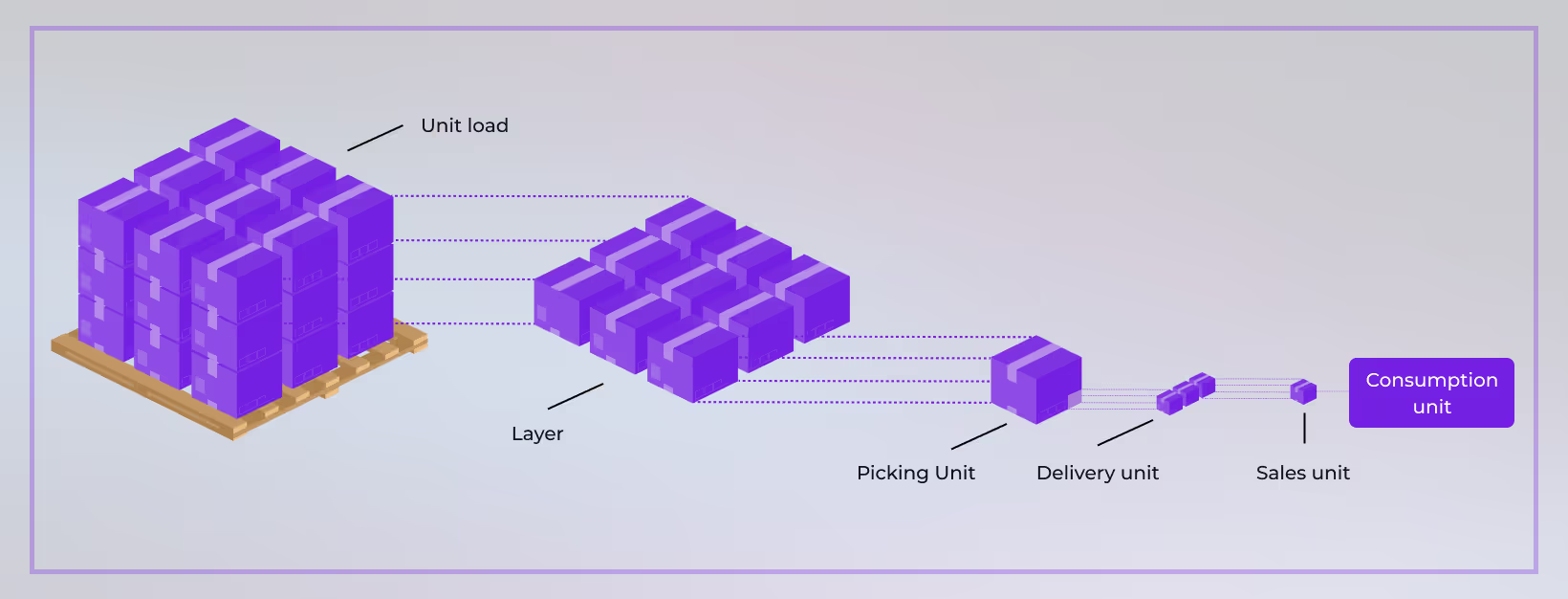
Types of Palletizing Solutions
Now that you know how to palletize, you should consider the best possible equipment for it. Each type is designed to suit specific production needs and logistical challenges. Here's a breakdown of the different palletizing solutions:
Manual Palletizers
This basic form of palletizing relies entirely on human labor. While they are cost-effective for small-scale operations, manual palletizing service is labor-intensive, time-consuming, and impractical for high-volume production lines.
Semi-Automated Palletizers
Combining human labor with automation, semi-automated systems improve ergonomics through tools like hydraulic pallet lifts and palletizing conveyors. So, these palletizing machines offer a middle ground, enhancing efficiency and reducing physical strain while maintaining a reasonable cost for moderate production volumes.
Palletizing Robots
Featuring robotic arms and customizable end-of-arm tooling, these systems are ideal for high precision and versatility. Robotic palletizing can handle a wide variety of products and patterns, making them popular in industries with diverse product lines and strict handling requirements.Â
The components of a robotic palletizer consist of an arm featuring an end effector or product gripper. This arm lifts items from a conveyor or layer table and places them onto a pallet. The end-of-arm tools can vary, including mechanical, suction-based, or magnetic grippers, depending on the specific needs of the handling process.
High-Level Palletizers
Positioned above the ground, high-level palletizers (or in-line palletizers) receive products from an elevated conveyor and place them on pallets. Due to their ability to handle high-throughput volumes efficiently, they are often used in industries with high-speed production lines, such as bottling plants.
Low-Level Palletizers
Operating at ground level, low-level palletizers are suitable for heavier products or industries with lower production volumes. They offer a more cost-effective solution for operations where high speed is not the primary concern, but handling heavier loads is.
Best Practices for Palletizing
Here are some ways to make sure that the palletizing process is as efficient as possible:
- Optimize Product Arrangement: Your pallet configuration should maximize stability and minimize wasted space. You can also use a pallet calculator to figure this out. Stack products uniformly and interlock them to prevent shifting during transit. Here are some tips for handling irregularly shaped products:
- Use specialized grippers that can adapt to the shape of the product.
- Develop specific palletizing layer patterns for irregular items and experiment for stability.
- Implement technology to visualize and optimize the palletizing process for irregular shapes.
There are three types of pallet stacking patterns that you can employ for the pallet arrangement:Â
- Column Pallet Stacking: Maintain the same footprint for stacked cartons.
- Brick Pallet Stacking: Alternate the footprint on each layer to create interlocking stability. This strong configuration reduces the number of boxes per pallet.
- Interlocking Pallet Patterns: Use a rotating stacking method for enhanced stability and support. It is best for higher-density loads, although it may reduce the total number of goods per pallet.
- Use proper pallets: Select pallets suitable for the weight and dimensions of the products. You also have to consider the material choice (wood, plastic, metal) based on load-bearing capacities and handling equipment.
- Secure loads: Use stretch wrap, banding, or strapping to secure loads firmly to the pallet. This prevents shifting or falling during transport, reducing damage and injury risks.
- Distribute weight properly: Material should be stacked so the weight is evenly distributed. This keeps the center of gravity low to prevent toppling.
- Labeling and documentation: Clearly label pallets with product details, quantity, and handling instructions for inventory management and minimizing errors.
- Training and safety: Train operators in proper palletizing techniques and safety measures. Ergonomic analysis can help reduce workplace injury risks.
The Path to Automated Palletizing
The evolution of industrial palletizing automation has been marked by significant innovation. Manual palletizing used to be the standard method, but it gradually transitioned to mechanical systems and, eventually, to fully automated solutions. Today, we're witnessing an exciting advancement in this field with robotic palletizers. These systems blend the efficiency of automation with the precision of cutting-edge robotics, paving the way for a new era in palletizing.Â
Benefits of Palletizing AutomationÂ
- Increases loading speed and turnover for perishable goods.
- Labor needs can decrease by 75% or more; often, only one operator oversees the palletizing process.
- Robots can work 24/7, allowing employees to focus on more value-added tasks while ensuring consistent productivity.
- Automated palletizing can save up to 50% of floor space, facilitating better organization and compatibility across supply chains.
- Speeds up delivery vehicle loading, improving fuel efficiency and reducing environmental impact.
How to Choose the Right Palletizing Solution for Your Needs
Selecting the right automated palletizing solution is critical for business efficiency. You should consider production volume and throughput requirements, which determine the palletizing equipment's capability. Assessing the product variability is also important as a versatile robotic system may be necessary for diverse shapes and sizes. Your floor space should fit nicely with the solution. Ensure compatibility with existing production systems and plan for future growth to avoid frequent upgrades.Â
Budget considerations should balance initial costs with long-term efficiency.
{{returns-webinar}}
Optimized Palletizing with PackageX
PackageX offers several solutions that can enhance warehouse operations and inventory management to support palletizing processes. For instance, our AI scanning technology automates data capture from various documents, helping you effectively track palletized items.Â
PackageX also provides inventory management solutions that enable real-time tracking and updates, along with warehouse automation technologies designed to improve overall efficiency. These solutions can be integrated into a larger warehouse management system to help optimize palletizing workflows.
FAQs Â
What is a palletizing system?
A palletizer is a machine designed to automate the sorting, transferring, and stacking of cases or products onto a pallet, typically at the end of a manufacturing line. This automatic process is especially beneficial for high-volume shipping, making it more convenient and efficient for businesses to manage their logistics.
Why do we palletize?
Palletizing is a great way to save space in your warehouse. By using vertical storage, you can make the most of your available space. Plus, optimized pallets can help you save on shipping costs. When products are stacked effectively, it not only makes for a more organized warehouse but also allows for more efficient shipping. It’s a win-win for both storage and logistics.Â