Returns have become an inevitable aspect of the retail industry, especially with the surge of eCommerce and the convenience of options such as 'Buy Online, Return in Store.' Shoppers are returning products at an unprecedented rate, leading to significant implications for retailers' profits. According to the 2022 Consumer Returns in the Retail Industry report, U.S. retailers suffered losses of $816 billion due to returns. Over the recent holiday season, a significant increase in returns was reported, with a year-over-year surge of 63%. This is why reverse logistics is a crucial part of the supply chain.
In this blog, we will explore reverse logistics, its definition, key components, and how it manages the flow of goods and materials from end-users back to manufacturers.
What Is Reverse Logistics?
Reverse logistics manages the flow of goods from their final destination to their point of origin, i.e., from shoppers to the sender or manufacturer. It involves various activities, including goods transportation, returns processing, and inventory disposition. Reverse logistics examples include product returns due to customer dissatisfaction, damaged or defective goods, overstocks, and expired products.
Reverse Logistics vs. Traditional logistics
In traditional product flow, goods move from suppliers to factories or distributors and then on to retailers and customers. Reverse logistics management begins at the consumer- moving products backward through the supply chain. This process may involve returning items to a specific point along the supply chain, such as a distributor or the original supplier.
Well-structured supply chains are adaptable and capable of handling reverse logistics efficiently. Products can either be sent one step back in the chain or returned all the way back to the manufacturer. Moreover, returned items might also be reintroduced into regular sales channels or sold at a discount through liquidators.
What Are the Types of Reverse Logistics?
There are different types of reverse logistics, also known as reverse logistics components. These components encompass various aspects of returns management, including return policies and procedures (RPP), remanufacturing, packaging, handling of unsold goods, and addressing delivery issues. Reverse logistics also cover leases, repairs, and product retirement processes.
1. Returns management
It is a fundamental aspect of reverse logistics that deals with product returns from shoppers and includes efficient collection, sorting, and inspection of returned items. An effective returns management system aims to minimize processing time, reduce shopper effort, and facilitate seamless return experiences, ultimately enhancing shopper satisfaction and loyalty.
2. Return policy and procedure
A well-defined return policy and procedure helps manage shopper expectations, ensuring that returns are handled consistently and in compliance with company policies. Retailers can minimize return-related misunderstandings and disputes by providing transparency and clarity, fostering a positive shopper experience.
3. Remanufacturing
Remanufacturing is an eco-friendly approach to reverse logistics, focusing on restoring returned products to a like-new condition. This process involves disassembling, repairing, and reassembling returned items, making them suitable for resale or reuse. Remanufacturing reduces waste and environmental impact and presents cost-saving opportunities for retailers through repurposing returned goods.
4. Packaging management
Proper packaging management is crucial in reverse logistics to protect, and transport returned items efficiently. Retailers should consider sustainable packaging solutions that minimize material waste while ensuring product safety during return logistics. Strategic packaging management reduces costs, optimizes logistics operations, and enhances environmental sustainability.
5. Unsold goods
In reverse logistics, handling unsold goods involves deciding whether to reintroduce these items into the market, liquidate them through discounts, donate them to charitable organizations, or dispose of them responsibly.
6. End-of-life (EOL)
End-of-life products refer to items that have reached the end of their useful life and cannot be refurbished or resold. Proper management of EOL products is essential to ensure environmentally responsible disposal or recycling.
7. Delivery failure
This type of reverse logistics deals with products that are not delivered to shoppers, returned to fulfillment centers, and shipped back to the manufacturer. However, retailers can manage delivery failures by addressing the issue and resending the item.
8. Rentals
It includes retrieving, inspecting, and refurbishing rental items after shoppers return them. Efficient reverse logistics in this context is critical for maintaining the quality and availability of rental inventory.
9. Repair and maintenance
Reverse logistics also encompasses the process of handling items that require repairs or maintenance. This involves managing the logistics of returning faulty or damaged items, diagnosing the issues, and ensuring timely repairs or replacements to meet customer expectations.
Why Is Reverse Logistics Important?
The goal of reverse logistics is to ensure a hassle-free and seamless returns experience for shoppers so they buy again and recapture value from products that have been returned, whether through refurbishment, recycling, or other means. It plays a vital role in the supply chain and offers several benefits, including efficient returns management, asset recovery, reduced operational costs, sustainability, and improved customer satisfaction. As businesses are seeing an increase in returns and high shipping costs are a major concern, streamlining returns management can help them reduce costs associated with shipping and processing returns.
Additionally, reverse logistics helps businesses recover valuable assets through refurbishing, or recycling returned products, reducing waste, promoting sustainability, minimizing losses, and improving profitability. It also improves shopper satisfaction by providing a hassle-free and quick return process that can build customer loyalty and increase revenue.
Benefits of Reverse Logistics
An efficient reverse logistics process offers several key benefits:
- Cost Reduction: Streamlined returns management reduces transportation, warehousing, and inventory costs. Companies can also recover value from returned goods through resale, refurbishment, or recycling.
- Enhanced Brand Reputation: Offering flexible returns strengthens a company’s image as customer-centric and reliable.
- Increased Customer Satisfaction: A smooth returns process improves the customer experience, leading to higher loyalty.
- Risk Mitigation: Proper handling of returned goods helps manage compliance and safety risks.
- Sustainability: Improvement in environmental responsibility as efficient returns reduce waste by facilitating recycling or refurbishing.
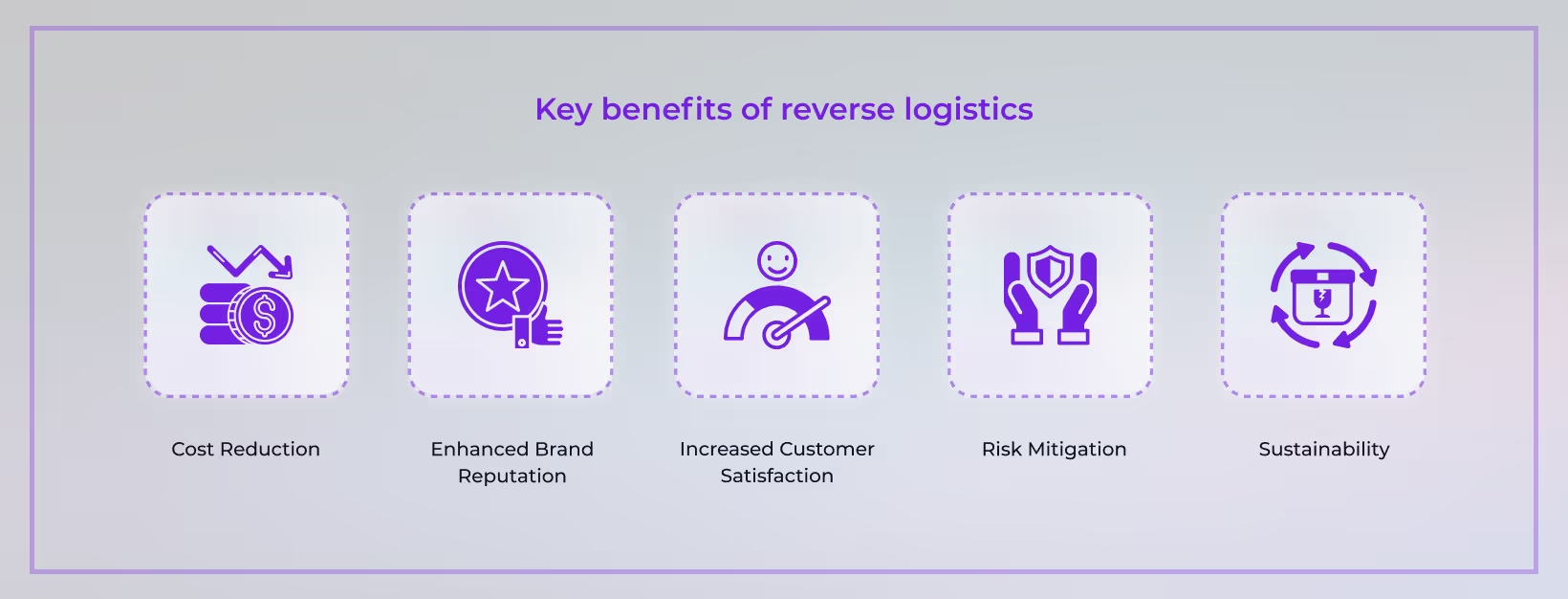
How Does Reverse Logistics Work?
Reverse logistics involves five stages: process the returns, determine the category, move the returns, execute the repair process, and recycle items.
1. Process the returns
The first stage involves receiving the return and determining its condition. Scheduling returns shipments and approving refunds is also a part of this stage.
2. Determine the category
The second stage involves categorizing the return based on its condition. The products are sorted into various disposition options such as fixing, reselling as new, reselling as a return, recycling, refurbishing, or scrapping.
3. Move the returns
The third stage involves moving the return to its appropriate destination, for example, sending the repairable item to the repair department.
4. Execute the repair process
The fourth stage involves executing the repair process if the return is repairable.
5. Recycle items
The final stage involves recycling the items that cannot be repaired.
How to Improve Reverse Logistics
To improve your reverse logistics process, consider these key strategies:
- Implement Clear Return Policies: Ensure your return policies are straightforward, efficient, and fair to customers.
- Include Return Labels: Add return labels to outbound packages to make returns easier for customers.
- Automate the Process: Use efficient reverse logistics solutions to automate your warehouse and returns management. Manual warehouse processes make retail returns costly due to labor inefficiencies. Automation offers a solution by improving accuracy and visibility. It also minimizes waste in tasks like receiving and inspecting. AI scanning is an effective way to automate without needing a complete system overhaul.
- This approach helps reduce manual errors while streamlining repetitive tasks.
- Centralize Returns: Establish uniform guidelines for all returns to streamline the process across products.
- Identify Return Causes: Gather customer feedback to understand why products are being returned, and address root causes to reduce future returns.
The Future of Reverse Logistics
The future of reverse logistics is about removing disruptions from the returns processes. More companies will invest in technology to improve reverse logistics processes, such as automated sorting systems and real-time returned product tracking. We may also see more partnerships between retailers and third-party logistics providers to streamline the returns process.
Trends and predictions for the future of reverse logistics include an increased focus on sustainability and environmental responsibility. Additionally, the emergence of new technologies like blockchain and artificial intelligence will continue to drive innovation in reverse logistics.
Optimize Reverse Logistics With PackageX
Reverse logistics can be a cumbersome and time-consuming process for many businesses. Whether dealing with returned goods, recycling materials, or excess inventory, managing the reverse logistics process can be challenging. However, with PackageX's innovative inventory management system, optimizing reverse logistics workflow has never been easier.
If retailers have brick-and-mortar stores, they can use PackageX Inventory at their returns drop-off points to receive returns, perform pick and pack, generate labels, and ship it back to the warehouse. However, if a retailer only has an online store and has partnered with a 3PL to handle returns, they can use Inventory once the item reaches their warehouse. Third-party logistics providers can also use PackageX to manage returns efficiently.
In addition to its reverse logistics capabilities, the PackageX Logistics Cloud offers a range of other features to help retailers streamline their logistics workflows. From automating package receiving and unifying inventory management to optimizing order fulfillment and shipment tracking, PackageX has everything retailers need to optimize first-to-last yard logistics operations and maximize efficiency.
{{returns-webinar}}
Reverse Logistics FAQs
What are the major issues in reverse logistics?
The major reverse logistics challenges include:
Warehouse Space : Reverse logistics often involves managing a diverse range of returned products, which can lead to storage space constraints. Retailers need to efficiently organize and manage warehouse space to accommodate returned items while optimizing inventory turnover.
Time and Costs of Damaged Returns: Processing damaged returns can be time-consuming and costly. Retailers must allocate resources to inspect, repair, or refurbish returned items to ensure they can be resold or reused.
Customer Expectations: Shoppers expect a hassle-free and prompt return process. Failing to meet their expectations can decrease customer satisfaction and brand loyalty.
Fraud: Reverse logistics processes can be vulnerable to fraudulent returns, where shoppers may attempt to return non-defective or used items for a refund. Retailers need robust fraud detection and prevention mechanisms to mitigate losses.
Complex Return Flows: Managing diverse return flows, including returns from retail stores, online sales, or third-party sellers, can be challenging. Each return channel may have unique requirements and logistics, making coordination complex.
What is the difference between reverse and traditional logistics?
Traditional logistics focuses on the forward movement of goods from suppliers to shoppers. Reverse logistics deals with the reverse flow of goods from shoppers back to suppliers for recycling, refurbishment, or disposal. So the reverse supply chain is almost opposite to a traditional supply chain; the product flows in a reverse movement.
What are the benefits of reverse logistics?
The benefits of reverse logistics include cost savings, enhanced shopper satisfaction, reduced environmental impact, improved inventory management, maximized asset recovery, better brand reputation, regulatory compliance, and supply chain optimization.
How does reverse logistics affect inventory?
Reverse logistics affects inventory by managing returned products, creating returns inventory, reducing shrinkage, optimizing inventory levels, facilitating refurbishment and resale, enabling recycling or disposal, tracking costs, improving customer service, providing data insights, and enhancing overall inventory efficiency.
What is a real-world example of reverse logistics?
A good example of reverse logistics would be returning unsold products from physical stores to distribution centers or handling product trade-ins, such as when a customer exchanges an iPhone 15 for an iPhone 16. These processes help you manage returns efficiently while also offering customers more flexible options for upgrades or refunds.