Inbound receiving, integral to last-mile operations, stores, and the warehouse receiving process, involves accepting and managing incoming shipments from suppliers and directing them to designated locations within the supply chain. This comprehensive process includes verifying the receipt of goods, conducting quality inspections, recording crucial data, and updating inventory systems.
However, several common mistakes can significantly hamper the efficiency of this process, leading to discrepancies in inventory records, delays in fulfilling orders, difficulties in maintaining optimal stock levels, and other operational inefficiencies that translate into lost time and money.
Read on to learn about ten of these mistakes and the practical inbound receiving solutions you can implement to address them, all of which are within reach and can be successfully integrated into your operations.
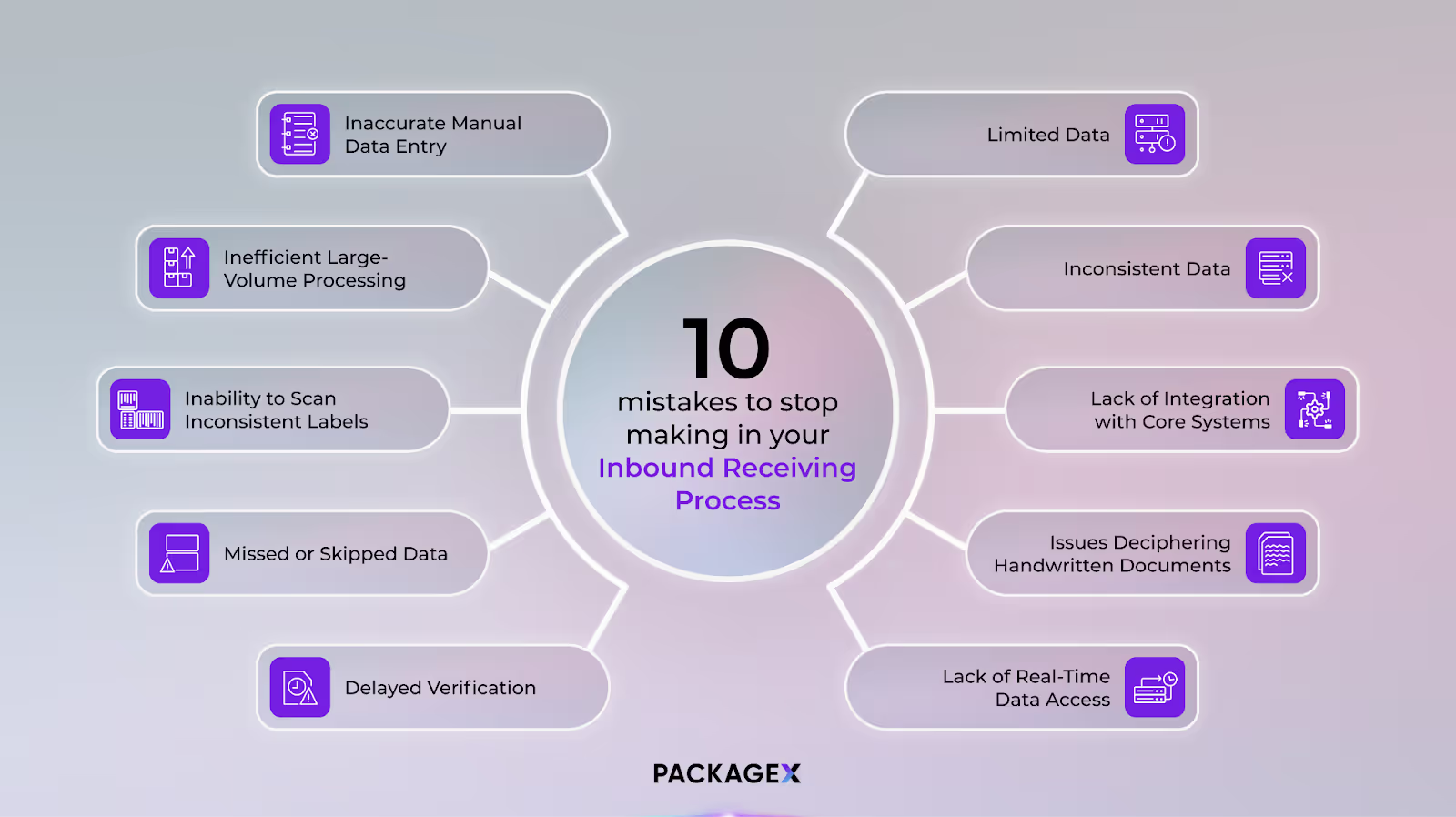
Mistake #1: Inaccurate Manual Data Entry
Relying on workers to manually enter data from important documents like shipping labels, invoices, and packing slips increases the chances of typos and missed entries.
This could lead to inaccurate inventory records, shipment discrepancies, and order fulfillment delays, negatively impacting customer satisfaction and operational efficiency.
Inbound receiving solutions:
- Implement automated data capture technologies like optical character recognition (OCR). Warehouse staff can use OCR scanners to automatically capture essential data from bills of lading, and shipping manifests without manual input, improving data accuracy and overall warehouse efficiency.
- Introduce validation checks at entry points to ensure data accuracy and completeness.
- Conduct regular audits of data entry processes to identify and address recurring issues.
Mistake #2: Inefficient Large-Volume Processing
Inadequate processes for handling large volumes of incoming goods, such as physically verifying each package and manually inputting data into a system, lead to errors, bottlenecks, longer processing times, shipment delays, and even higher labor costs.
Nowhere are these shortcomings felt more than with inbound receiving at last-mile operations, where a considerable volume of packages are handled before shipment to the end customer.
Any flaws in the process are quickly exposed. Imagine having to physically handle, verify, and input data from thousands of packages before final shipment to the consumer.
Solutions:
- Implement batch processing techniques and scalable infrastructure to handle peak loads efficiently.
- Invest in automation to streamline inbound receiving and reduce processing times. For example, you can use OCR to automate data capture at scale. The right OCR software uses AI to combine QR, text, and barcodes to collect all information on the label in just seconds.
Mistake #3: Inability to Scan Inconsistent Labels
It’s not uncommon to encounter label inconsistencies during the inbound receiving process. These can range from damaged labels that are hard to read to handwritten formats that vary in legibility to labels that deviate from expected design layouts.
Without robust scanning capabilities, these inconsistencies lead to data entry errors and processing delays. Many warehouses, for example, rely solely on barcode scanners, which can only encode a limited amount of information and struggle when a label is damaged.
Solutions:
- Train staff to handle ambiguous or damaged labels.
- Standardize labeling practices with suppliers to maintain consistency and minimize delays.
- Implement OCR software as it can accurately interpret diverse label formats. Unlike barcode scanners, it enables smartphones to function as universal label scanners, capable of scanning in low light and reading damaged labels.
Mistake # 4: Missed or Skipped Data
Failing to capture the necessary data during the receiving process leads to incomplete records and the loss of critical data. This missing data can significantly impact inventory management and order fulfillment decisions, leading to inefficiencies, errors, and potential disruptions in the supply chain.
Solutions:
- Introduce standard verification steps and processes to capture all data.
- Enhance warehouse management software (WMS) with automatic data capture technologies to handle complex data requirements.
- Invest in automation and technology, such as OCR software and RFID technology, to minimize human error and ensure data completeness.
Mistake #5: Delayed Verification
Not promptly conducting checks and inspections on received goods after they arrive in the warehouse leads to inventory inaccuracies and potential fulfillment errors.
Common causes for delayed verification include an overreliance on visual inspections, a lack of automation, and insufficient resources to handle volumes, especially during peak periods.
Solutions:
- Introduce a comprehensive verification checklist that includes the quantity, quality, and condition of goods to ensure thorough inspections.
- Use a WMS to implement automated alerts to identify and resolve discrepancies quickly. For instance, you can trigger alerts for mismatched quantities or damaged goods.
- Create dedicated verification stations equipped with the necessary tools and technologies, like OCR software, to accelerate package verification. In logistics, OCR’s verification capabilities can also help maintain regulatory compliance by facilitating quick scanning and cross-referencing of important documents to ensure they meet required standards.
Mistake #6: Limited Data
If you’re using basic scanning technologies, like barcode scanners, you’re likely only capturing basic information during the receiving process, such as item names and quantities. Barcode scanners encode limited amounts of data, failing to capture crucial data like sender/carrier information and item condition.
As a result, you’re probably not gathering the data you need for comprehensive inventory management. Without batch numbers, for example, it’s difficult to track expiration dates, which can lead to inventory wastage.
Solutions:
- Expand your data capture capabilities to include essential data like batch numbers, expiry dates, and quality metrics.
- Implement versatile systems and technologies, like OCR software, to capture and encode extensive information accurately.
Mistake #7: Inconsistent Data
Not having standardized data entry protocols can lead to inconsistencies in how staff record and interpret data. This issue is often more pronounced when relying on manual inputs, where human variability can play a large role.
For example, different employees may use inconsistent abbreviations when recording quantities such as “Qty,” “QTY,” or “Quantity.” These inconsistencies complicate data analysis, reporting, and decision-making.
Solutions:
- Develop standard data entry formats across all receiving processes for key data fields.
- Conduct regular audits to identify discrepancies and ensure compliance with protocols.
- Use OCR to validate and standardize data entry formats automatically. OCR validates the data for accuracy by checking that it matches the predefined standards and automatically converts varied formats into standardized fields to maintain data integrity.
{{returns-webinar}}
Mistake #8: Issues Deciphering Handwritten Documents
Depending on manual interpretation of handwritten documents, which vary in legibility, can lead to errors like order fulfillment mistakes, processing delays, and miscommunication with suppliers due to ambiguity, potentially resulting in disputes with suppliers.
Solutions:
- Implement automated text recognition tools to quickly convert handwritten text into digital formats to reduce errors resulting from manual input.
- Establish standard procedures for processing handwritten documents. For example, establish processes for cross-checking and verifying OCR results against original handwritten documents.
Mistake #9: Lack of Integration with Core Systems
Inbound receiving processes that are not integrated with core systems result in duplication of work and data, fragmented workflows, and data silos. Data silos limit visibility into the supply chain and make it challenging to maintain a holistic view of your operations.
For instance, inventory levels may not be accurately reflected across all systems, with your WMS showing something completely different from your ERP system. This can lead to stockouts or overstocking situations.
Solutions:
- Connect inbound receiving systems with ERP and CRM software to ensure seamless data flow and synchronization across systems. APIs (application programming interfaces) can help you do this.
- Use OCR for specific functions, such as integrating digitized invoices with your ERP system to maintain financial accuracy.
- Enhance warehouse management processes by digitizing receiving data during inbound receiving and connecting it with WMS software.
- Scan and process return label information and integrate it with digital returns portals, WMS, and Inventory Systems to streamline the returns process and ensure returned products are quickly logged back into the system.
Mistake #10: Lack of Real-Time Data Access
Without timely access to important receiving data like shipment details, returns, and invoice information, you hinder your ability to quickly react to changes in inventory, supplier updates, and customer needs. This delay in decision-making can lengthen lead times and lower operational efficiency overall.
Solutions:
- Improve data capture speed and accuracy with OCR technology. OCR technology quickly and automatically extracts and digitizes data from scanned documents and labels, providing timely access to crucial information.
- Integrate OCR with your core systems for smooth data transfer and real-time data access. Scanned data, such as package identification numbers, recipient addresses, and delivery statuses, are instantly available in ERP or WMS systems to help with agile decision-making.
Avoid Common Inbound Receiving Mistakes Today
Inbound receiving is a critical component of supply chain management, but common pitfalls like inaccurate data entry, delayed verification, and lack of real-time access often undermine it.
However, by implementing the right inbound receiving solutions, such as OCR document scanning software, you can automate data capture and enhance accuracy, overcoming these costly errors to run a more efficient and profitable operation.
One such solution is PackageX. PackageX offers an advanced inbound receiving solution designed to automate, digitize, and streamline the receiving process.
Using AI-powered OCR technology, PackageX accurately captures, processes, and integrates data from incoming shipments into existing systems without manual input.
The result? Improved data accuracy, enhanced operational efficiency, and real-time access to critical information—even when operating at scale.
Explore how PackageX can transform your operations today with a demo.