An efficient warehouse layout optimizes space, productivity, and safety. A well-designed warehouse layout makes it easier to store, locate, and manage goods so you can achieve:
- Streamlined workflow
- Minimized wasted time
- Reduced operating costs.
Areas like dynamic and static storage, shipping, and receiving must be configured to meet space and product throughput needs. If you’re setting up a new warehouse or reorganizing an existing one, keep reading this blog to find out how you can maximize space, reduce handling, and ensure easy product access. All these are essential elements for maintaining a fast, flexible, and cost-effective supply chain.
What Is Warehouse Layout?
Warehouse layout refers to the physical structure of your warehouse and the arrangement of all its components. A well-organized warehouse layout gives workers enough space to operate efficiently while allowing for a faster, smoother inventory flow.
What Are the 5 Areas of a Warehouse?
If you’re wondering what a warehouse looks like, there are five main areas that the warehouse layout establishes:
Loading and Unloading Area
This area is crucial for the reception and dispatch of goods. If it’s well-integrated into the facility, it provides direct access for transport vehicles, such as trucks, trailers, and containers, making the movement of goods more efficient.
Receiving area
The receiving area is typically located inside the warehouse, which is usually connected to a receiving bay on one side, allowing trucks and transport vehicles direct access.
To streamline operations, the receiving area should be positioned close to the storage area so that goods can move easily to their designated locations. This warehouse setup is particularly important unless the warehouse primarily focuses on cross-docking, where quick transfer of goods is the priority.
Storage area
The storage area in a warehouse is where inventory is held until it's needed for order fulfillment. A storage area must be easily accessible as it typically features pallet racks and shelving units and is strategically connected to both the receiving and packing areas. A well-organized storage area improves order-picking accuracy, reduces travel time, and improves overall inventory management, making it one of the most critical yet complex sections of the warehouse. The most costly activity in the typical warehouse is order-picking. You should understand item rotation needs and the types of goods stored to optimize this space.
There are two types of warehouse storage layout design. Dynamic storage, also known as forward pick, is where high-demand items are picked for orders, with multiple rack types used to reduce pick time. It prioritizes quick access and efficiency. Static storage, or reserve storage, holds overflow products on pallets, providing high-density storage for replenishing the dynamic area when needed. Both warehouse layouts enhance warehouse efficiency by balancing immediate access with space optimization.
Packing area
This area is dedicated to product packaging before shipment. It is typically equipped with all the necessary packing materials, tools, and equipment to ensure items are securely packaged for delivery. The warehouse packing station layout is designed so that it has direct connections to both the storage area and the shipping bay, allowing for efficient movement of goods. By facilitating a smooth packing process, orders are prepared quickly and accurately, contributing to effective overall warehouse operations.
Shipping area
The shipping area is the opposite of the receiving area- outgoing orders are prepared for shipment here. Located inside the warehouse, this area typically connects to a shipping bay on one side and has direct access to the parking area on the other. A well-planned warehouse layout includes space for wrapping pallets and accommodating equipment like pallet jacks and forklifts. There should be room to stage completed orders that are ready to be loaded onto trucks for distribution.
Factors to Consider for Warehouse Layout Design
Designing a warehouse layout involves several key considerations unique to each business.:
- The type of operation, available space, equipment needs, workflow, safety regulations, and cost efficiency all influence the warehouse layout design phase. Moreover, warehouse design must consider product characteristics.
- The warehouse layout should match the business’s operations, whether it’s manufacturing or distribution, and maximize the use of available space during warehouse planning.
- Proper storage solutions, material handling equipment, and an organized warehouse layout for workflow help boost productivity and minimize errors.
- Ensuring compliance with safety regulations and balancing costs with operational goals is essential for creating an efficient, well-functioning warehouse.
How to Start Warehouse Planning
Designing a warehouse layout involves careful planning to ensure efficiency and safety. Here are five essential steps:
- Equipment Requirements: Plan for the space needed to accommodate equipment like forklifts and pallet jacks. Considering this from the start helps prevent overcrowding and leads to smooth operations.
- Products: Think about product types, warehouse size, and weights. This way, you can design suitable storage areas and organize items for easy access. Define the warehouse’s purpose and business model- the facility layout depends greatly on the processes that are to be performed.
- Space and Volume: Create a 2D diagram and calculate total storage space. Based on inventory, consider storage requirements and calculate the pallet racking layout required.
- Assess Personnel: Ensure your team has adequate space and training to operate safely and efficiently.
- Product Flow: Minimize product handling by optimizing the warehouse layout for smooth circulation, reducing time and effort for moving goods. Test traffic flow with a mockup of aisles and pathways. One of the benefits of a well-designed ergonomic work environment is low operating costs.
What Are the Types of Warehouse Layouts?
When designing a warehouse, the three common product flow layouts are:
- A U-shaped warehouse layout is the most popular warehouse layout. Its shipping and receiving docks are placed next to each other, allowing for shared resources and minimizing product handling.
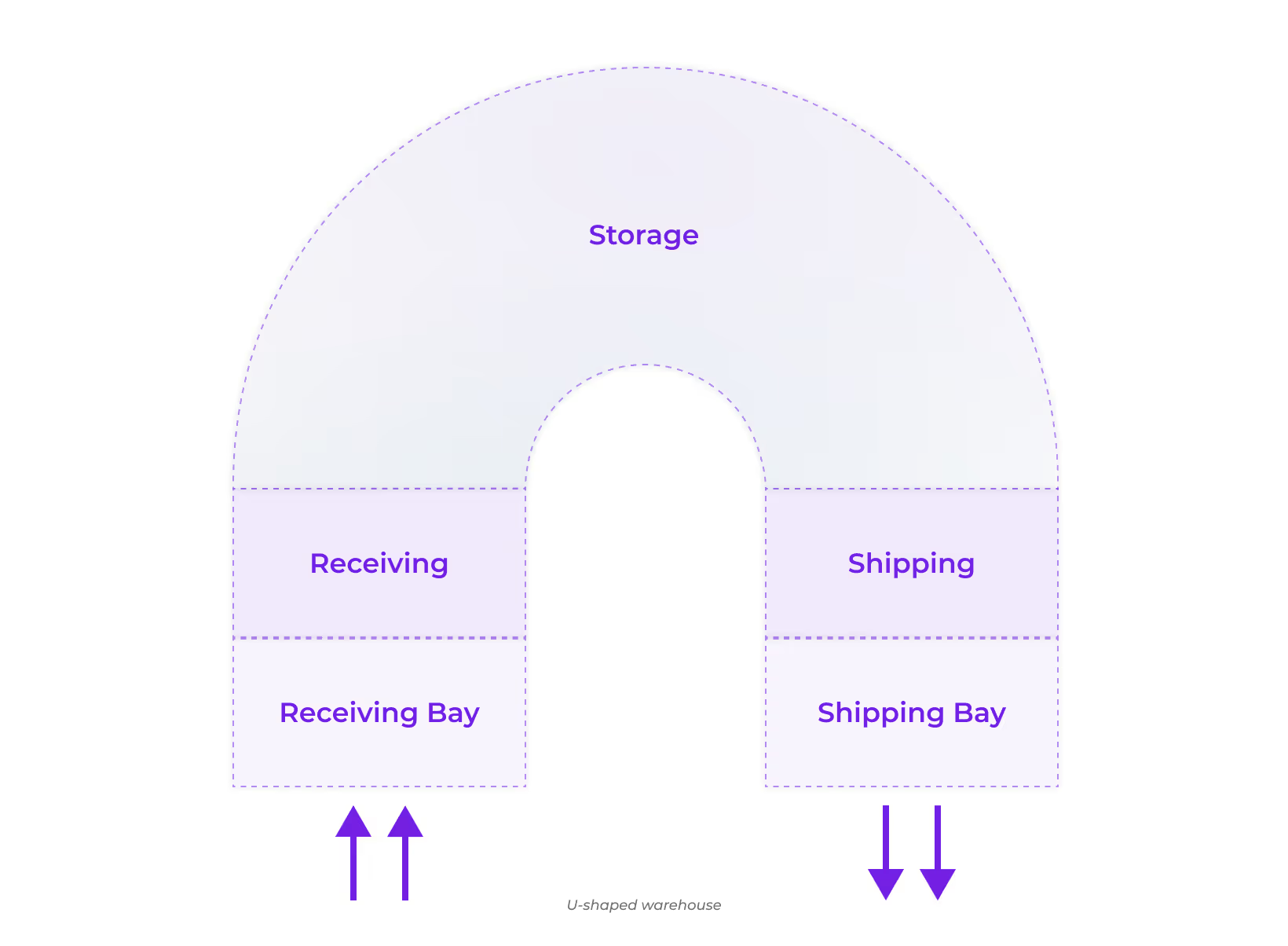
- In an I-shaped warehouse layout, shipping is at one end, receiving at the other, and storage in the middle. This arrangement is ideal for high-volume, assembly-line-style operations.
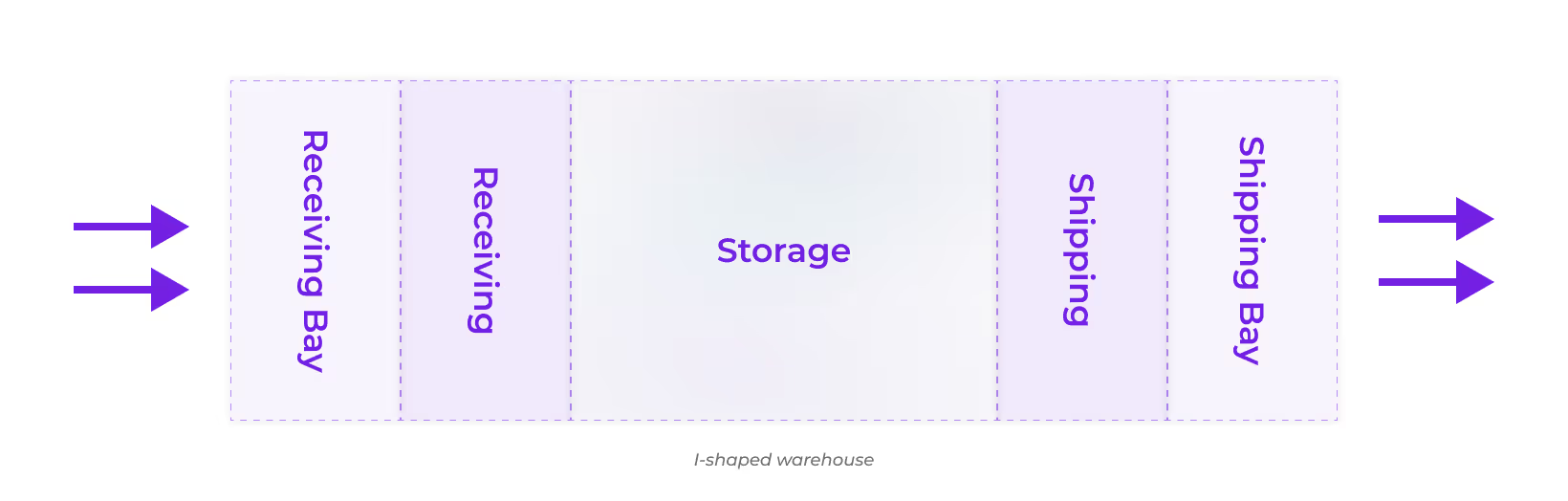
- An L-shaped warehouse layout positions shipping and receiving on adjacent walls, creating a 90-degree angle. This warehouse layout design suits businesses that need cross-docking to move goods quickly from inbound to outbound trucks.
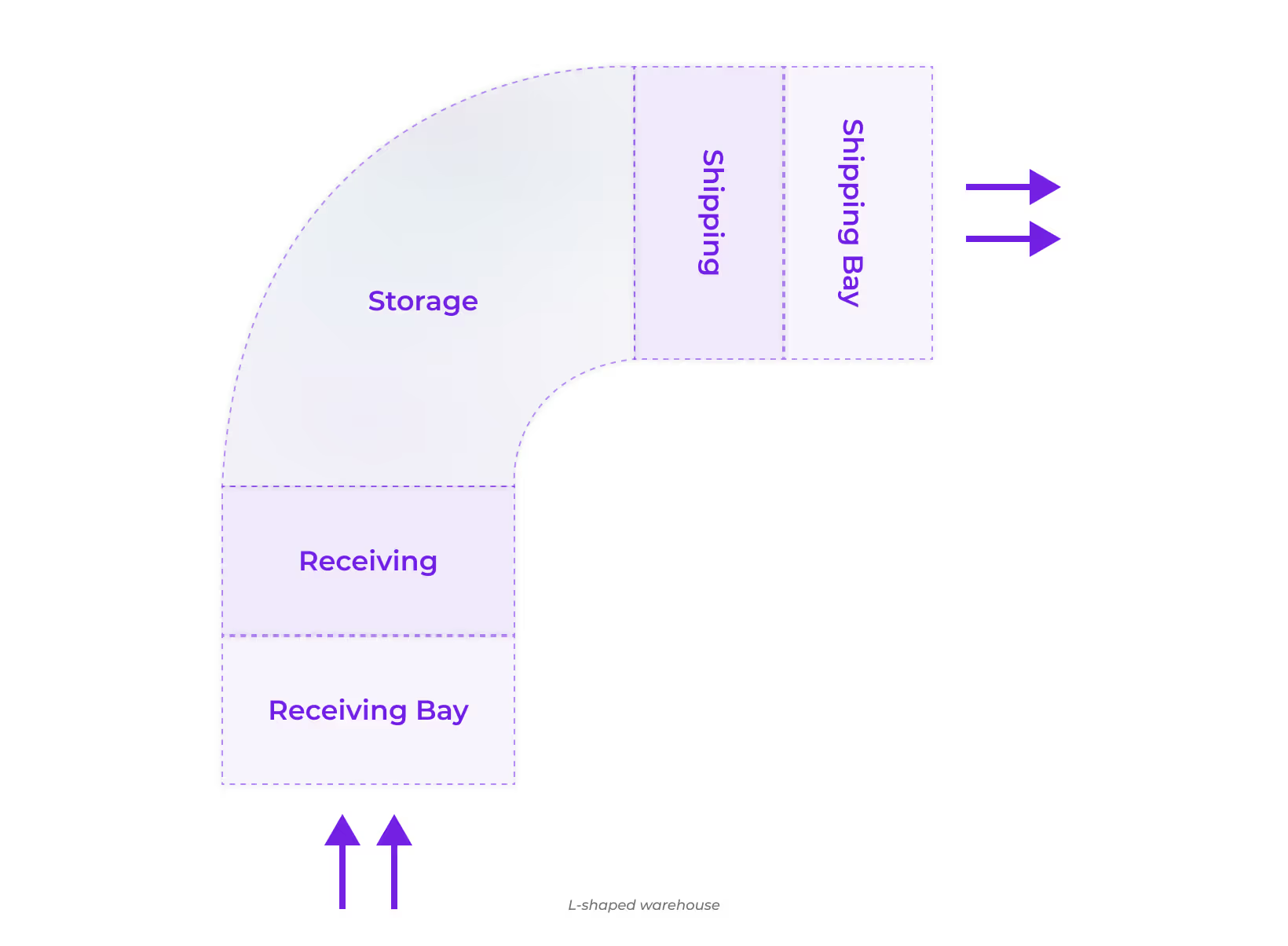
Warehouse Layout Best Practices To Follow
- Warehouse Space Optimization: Utilize vertical storage with adjustable warehouse racking design systems. Stack pallets where it’s safe to reduce the need for additional shelving.
- Product Accessibility and Visibility: Design clear paths from receiving to shipping and use appropriate lighting, labels, signage, and color codes for quick inventory access.
- Plan for Future Change: Design with flexibility to accommodate growth and operational changes so that space can be reallocated as needed.
- Incorporate Technology: Use warehouse management systems (WMS), inventory tracking, automated systems, and RFID to boost efficiency and accuracy.
- Prioritize Safety and Cleanliness: Keep the warehouse clean, reduce clutter, follow safe practices defined by warehouse design standards, and provide staff training to prevent accidents and maintain compliance.
- Continuous Optimization: Review performance data regularly, adapt warehouse layouts based on operational needs, and stay informed about new technologies like drones and automation.
What Are the Challenges of Warehouse Layout Design?
Designing and implementing warehouse equipment comes with several challenges. It takes a lot of time and requires precise planning for warehouse space management while staying cost-effective. Structural issues, like poorly placed shipping and receiving bays or uneven flooring, can cause bottlenecks or safety hazards. Safety and compliance are also major concerns, as warehouses can be hazardous due to heavy machinery, high shelving, and the handling of dangerous materials. You must prioritize proper worker safety protocols and meet industry standards to create a secure working environment.
Achieving Warehouse Layout Optimization With PackageX
Technology plays a vital role in warehouse layout optimization; for instance, PackageX’s Warehouse Management System (WMS) can identify inefficient warehouse layouts and suggest optimal storage locations, enhancing productivity. Warehouse layout optimization often requires analyzing current throughput, understanding product needs, and selecting appropriate storage systems.
Organizing the space into distinct areas for receiving, storage, order processing, packaging, and returns can streamline operations. Implementing yard management is essential for monitoring loading dock activities and preventing bottlenecks. Businesses should consider warehouse automation to increase productivity and safety while considering future growth.
{{returns-webinar}}
FAQs
What is the most efficient warehouse layout?
U-shaped warehouses are among the most common warehouse layout designs and are commended for their efficiency. I-shaped warehouses are ideal for larger businesses, providing ample space for operations. On the other hand, L-shaped warehouses are usually employed to fit into existing structures, making them a practical choice for certain environments.
What are the objectives of warehouse layout?
Regardless of the reason for the warehouse layout design, it must achieve a few key objectives: maximize the available space, minimize the number of movements and distances traveled during load handling, and ensure easy access to the products.