Introduction
Regardless of their success, retailers must deal with one inevitability: returns. Sales, especially in ecommerce, continue to grow. But with that growth also comes growth in returns. According to the National Retail Federation, the total return rate for retail purchases in the United States in 2023 was 14.5% of sales, amounting to $743 billion in returns.
In 2020, 2021, and 2022, stay-at-home mandates and social distancing restrictions from the COVID-19 pandemic made ecommerce sales soar. The result was quick adaptations by retailers looking to improve the customer experience for shoppers who initiate returns. Many swiftly implemented advanced returns software, including free returns options, buy-online-return-in-store (BORIS), and more.
Every 3 in 10 people who purchase an item online will return it, so it makes sense that retailers would optimize and simplify the customer experience during the returns process. Otherwise, consumers who find the returns process overly complicated would not make future purchases. However, many retailers have prioritized the customer experience and deprioritized profitability, sinking major costs into overlooked areas of reverse logistics.
With the rate of returns outpacing the rate of sales in ecommerce, retailers should now consider returns a major cost center. Not only are they losing revenue from the cost of the sale, but manual receiving and restocking processes result in efficiencies and mounting labor costs. According to research by Narvar, it costs retailers $33 to process a return when costs related to labor, shipping, postage, fraud, and more are all tallied up.
Are you a visual learner? We got you. Check out our on-demand webinar, Returns Revolution: Unleash Warehouse Efficiency with Automation.
The Hidden Culprit: Manual Processes
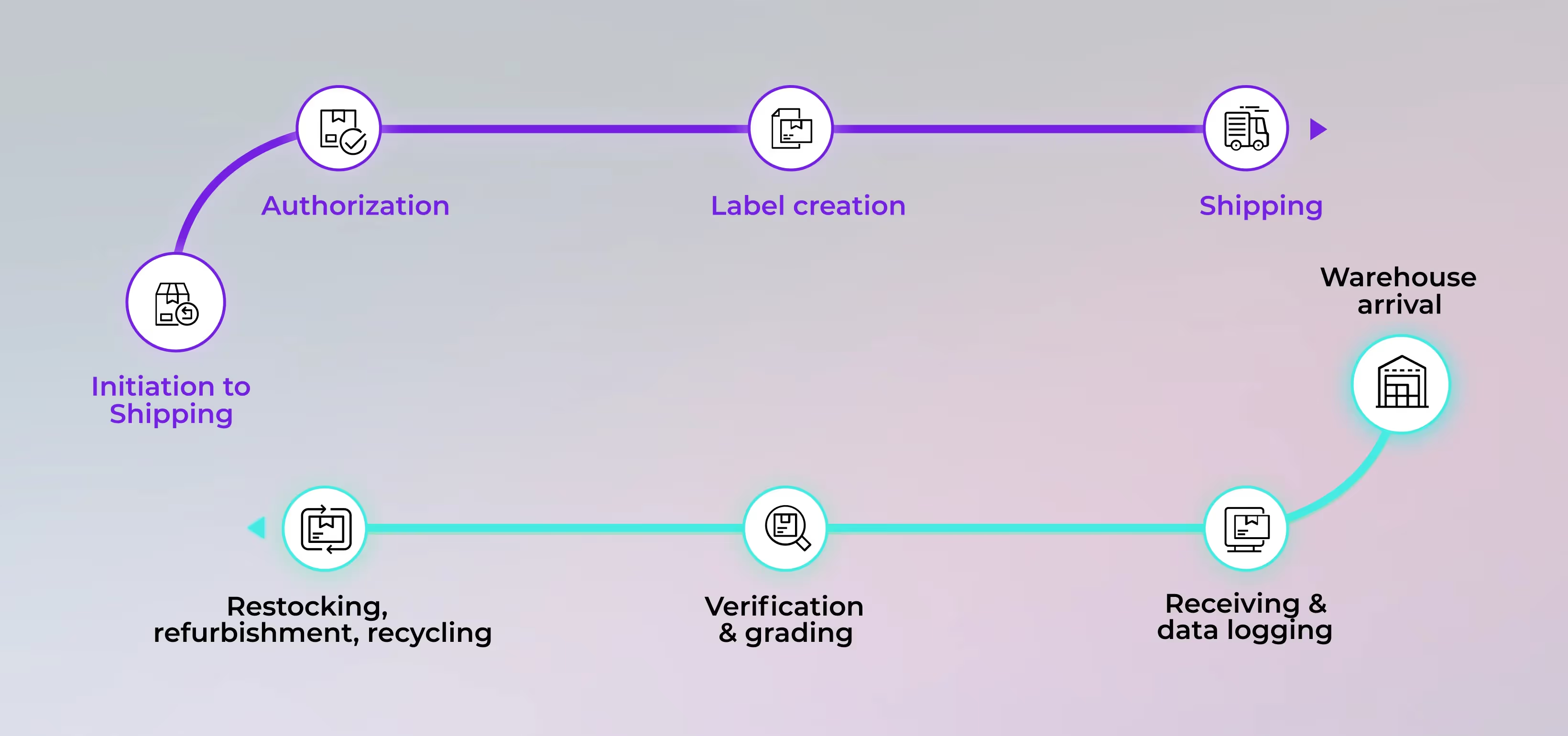
More than half of the costs associated with returns happen during the second leg of the returns journey. While many retailers focus most of their efforts on optimizing for the initiation to the shipping stage of reverse logistics, ¾ of the costs are associated with what happens to returns after they arrive at the warehouse. This is because manual processes and disjointed systems draw out the returns process, forcing retailers to pay more and longer warehouse wages.
The Power of Warehouse Automation in Reverse Logistics
After an explosion of ecommerce sales (and returns) during COVID, many retailers focused on adding automation to the customer experience. This included adding intuitive returns portals or flexible returns options (shipping, Buy Online Return in Store, etc).
However, as we discussed, most return costs come from labor costs at the warehouse. Automation can help retailers make their workforce more productive and reduce costs. The potential for automation to improve warehouse labor productivity and throughput is why the market continues to grow. The warehouse automation market is expected to reach $71.01 billion by 2032 at an average annual growth rate of 15.91%. In addition to alleviating the costs associated with labor, warehouse automation can help:
- Increased Throughput and Fewer Errors: After introducing automation, your warehouse can handle a higher volume of returns, cut down on processing times, and reduce backlog. Machines can perform repetitive tasks associated with inventory management, material handling, receiving, fulfillment, and more accurately, leading to quicker and more effective processing.
- Better Visibility and Tracking: Warehouse management systems (WMS) provide immense value for managing operations involving returns, but they do have limitations around visibility and tracking. Integrating automation systems with your WMS can give you better visibility into the status of returns, helping you answer questions like, “Have they arrived at the warehouse? Have they been inspected? Were they restocked or disposed of?”
- Minimized Waste: Improved accuracy in retrieving, inspecting, sorting, and disposal can help reduce product damage and waste. Automation can efficiently determine what items must be recycled or resorted, enabling proper disposal and material reuse standards.
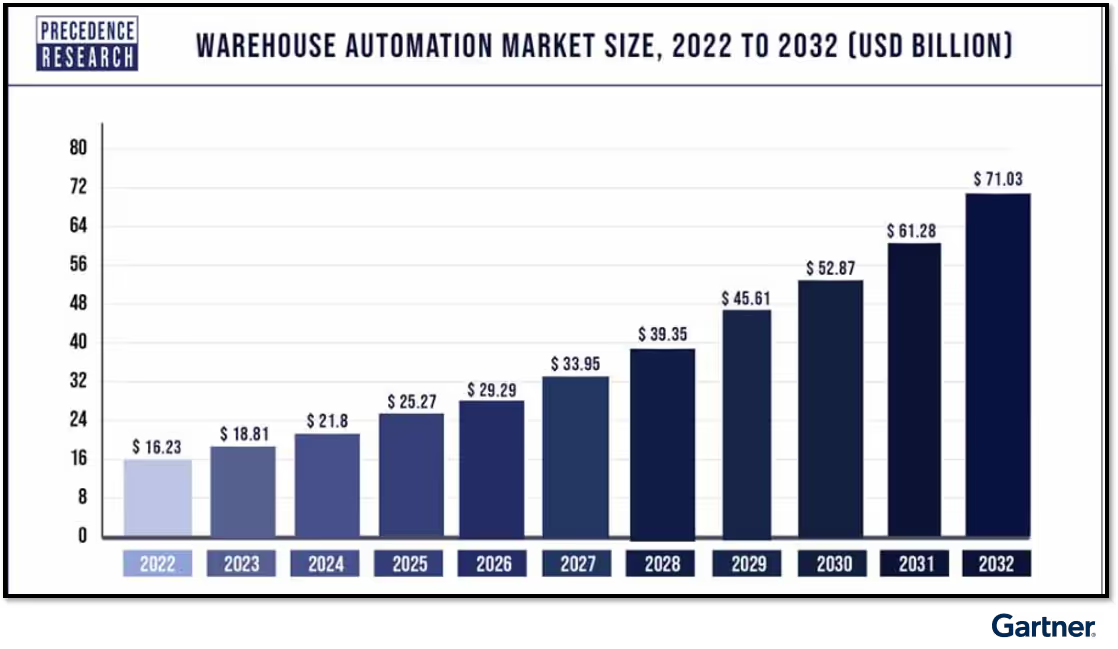
Warehouse Automation Solutions - AI Scanning & Receiving
One of the easiest ways to integrate automation solutions without overhauling entire processes is through AI scanning OCR technology for receiving and product verification. PackageX OCR technology is built with warehouse operations in mind. Users can choose to implement a full solution for receiving-to-disposal workflows or utilize our flexible APIs to complement or fill in data gaps with their existing technology stack (WMS, IMS, ERP, etc.). Here’s how warehouse operations can be enhanced with AI scanning automation:
- Automating data entry during receiving: Rather than manual efforts or traditional barcode scanning hardware, AI-powered OCR scanning can take high-resolution images of labels, Bill of Ladings, manifests, and more at the warehouse, capturing crucial information in seconds, including serial numbers, batch codes, expiration dates, QR codes, damage codes, and more. The captured images are fed into an AI engine trained on millions of labels and other packaging datasets, including handwritten data, low-light images, and more. The AI uses its preexisting knowledge to “clean” and sort data and automatically populates relevant systems (WMS, IMS) with the data in real time.
- Product verification and grading with AI-powered image recognition: Manual inspection is often slow and disconnected from the warehouse’s existing tech stack and sorting processes. In the same way AI can be trained on label scanning, it can be trained to analyze returns on a conveyor belt for defects, missing components, wear-and-tear, and more. Automation can then be added to direct the item to the right process: restocking, repair, or recycling.
{{returns-webinar}}
Returns Automation at the Warehouse
Manual warehouse processes turn inevitable retail returns into a cost center; labor costs driven by manual warehouse processes are inefficient and expensive. Warehouse automation is a powerful solution for repetitive tasks, including steps involved in receiving and inspecting, because it improves accuracy, enhances visibility, and minimizes waste. AI scanning is a great way to introduce automation to warehouse processes without overhauling entire systems.