Summary
- Warehouse management involves overseeing and optimizing all aspects of warehouse operations. It’s a critical business function for improving inventory accuracy, space utilization, labor costs, and resilience to supply chain disruptions.
- A warehouse management system (WMS) is a software solution that optimizes warehouse operations.
- Modern companies must adopt a holistic approach to warehouse management that incorporates technology-powered strategies, such as implementing a WMS, data analytics, automation, IoT, and smart warehouses.
PackageX is a complete, all-in-one logistics platform equipped with advanced scanning and receiving technologies to power your warehouse operations.
If there’s one thing made abundantly clear from the COVID-19 pandemic and its aftermath, it’s that efficient warehouse operations can have an outsized impact on the health and resiliency of your organization. Soaring consumer demand exposed weak points across supply chains, creating bottlenecks, labor shortages, and shipping delays. According to the Federal Reserve Bank of New York, global supply chain pressures peaked in 2022 before achieving some level of normalcy in 2023. Those with efficient warehouse management were better equipped to navigate disruptions, cut costs, and deliver superior service to customers.
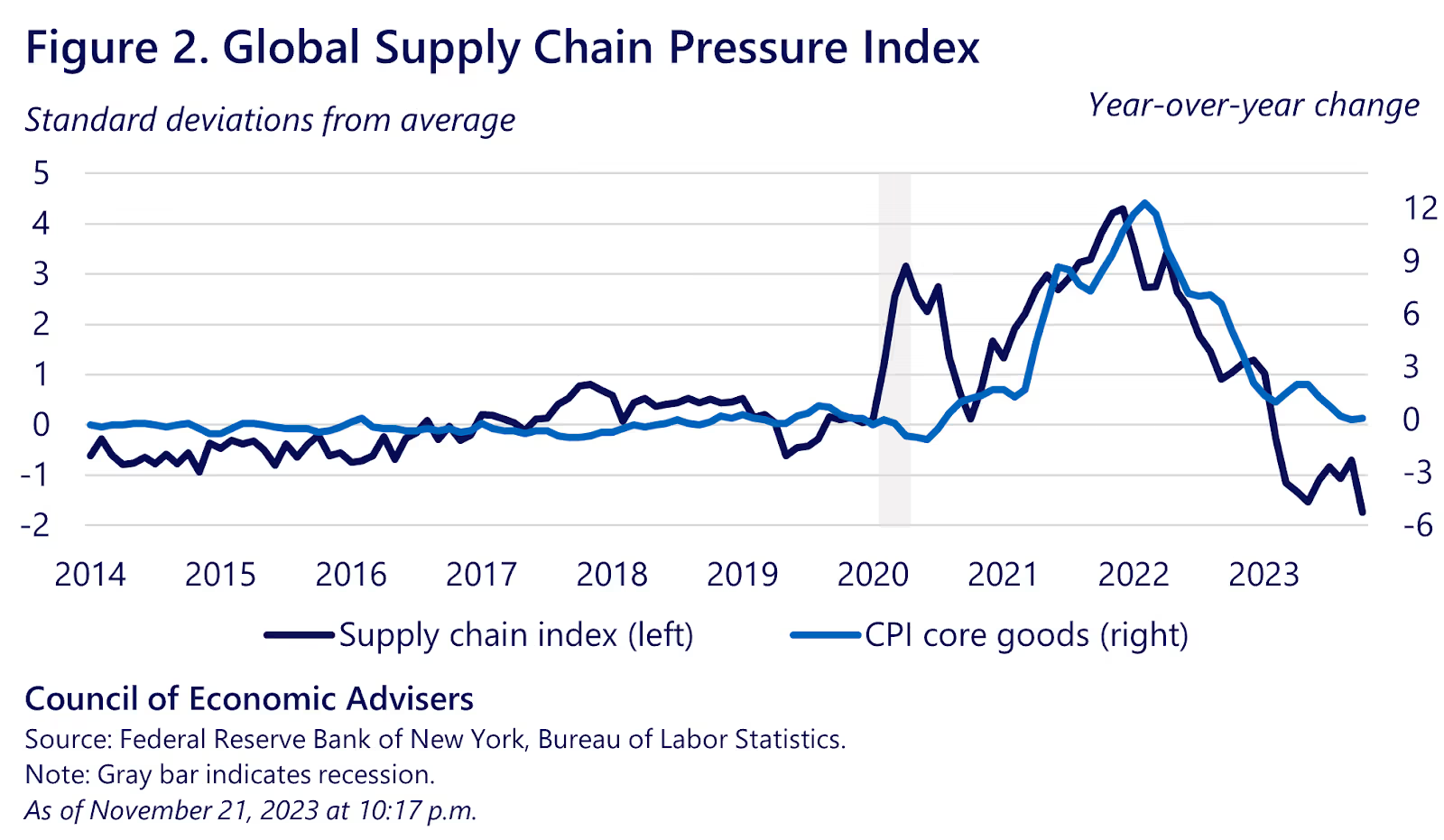
However, supply chains today still remain fragile. The shift from “just in case” inventory stockpiling to “just-in-time” inventory management is gaining momentum, and themes like nearshoring, automation, supplier diversification, and sustainability are forcing businesses to rethink the way they run their warehouse operations.
With all of these changes, how should businesses adapt while strengthening operations and building a more resilient supply chain?
A better way to optimize warehouse operations
Today, companies need to embrace a more holistic approach to warehouse management that combines technology with data-driven strategies. By implementing advanced warehouse management systems (WMS), automation, and following best practices, companies can not only improve efficiency but also create a durable competitive advantage by getting products to customers quickly and accurately. Real-time visibility and control over inventory also frees up working capital that can be reinvested back into the business.
In this guide, we’ll go over what you need to know about optimizing warehouse management. From improving inventory accuracy and enhancing order fulfillment speed to reducing costs, here are some of the most effective strategies and best practices to help your business succeed.
What Is Warehouse Management?
Warehouse management overseas the various operations within a warehouse, including receiving, storing, picking, packing, and shipping goods. These core functions are crucial for maintaining accurate inventory levels and ensuring timely deliveries.
Warehouse management plays a critical role in the movement of goods. Today’s customers demand faster delivery, service engineers require urgent spare parts, and retail partners want to cut costs. In addition to storing products, warehouses play a key role in optimizing fulfillment. Automating warehouse operations help businesses:
- Eliminate manual processes
- Reduce errors
- Prevent bottlenecks
- Forecast demand
- Limit stockouts and overstock
- Improve order fulfillment speed and accuracy
- Optimize space utilization
- And more.
Types of warehouses
There are several types of warehouses within the logistics network. These include:
- Distribution centers: Facilities focused on efficiently receiving, storing, and quickly distributing goods to retailers or customers.
- Public warehouses: Storage facilities available for rent by various businesses, typically managed by third-party providers.
- Private warehouses: Owned or leased by a company to store its goods exclusively, offering control over operations and layout.
- Bonded warehouses: Secured warehouses for imported goods, where taxes are deferred until the goods are released.
- Smart warehouses: Technology-driven warehouses using automation and IoT for improved efficiency and inventory accuracy.
- Climate-controlled warehouses: Facilities with temperature and humidity control, ideal for sensitive goods like electronics or pharmaceuticals.
- Fulfillment centers: Warehouses specialized in order processing and delivery, often linked to e-commerce operations.
- Cold storage: Refrigerated facilities for perishable goods, maintaining temperatures to preserve food and other temperature-sensitive products.
Each model is suited to different business needs and some of these warehouse types can be combined. For example, you can have a smart fulfillment center or a cold distribution center.
Why is warehouse management important?
Efficient warehouse management is crucial because it directly impacts inventory accuracy, space utilization, labor costs, and resilience to supply chain disruptions.
- Inventory accuracy: According to CSCMP's 2023 State of Logistics Report, the U.S. saw a 19.6% increase in business logistics costs in 2023, with inventory carrying costs making up 52% of that rise, underscoring the need for precise inventory control.
- Space utilization: According to Gartner, more than 75% of companies are expected to adopt automation in warehouses to optimize space and efficiency by 2027.
- Labor costs: Labor shortages also remain a challenge, with 57% of supply chain executives reporting difficulties meeting demand due to workforce constraints.
- Supply chain resiliency: Over the past two years, Gartner found that 73% of companies have restructured their supply chain networks, driven more by risk management needs. In fact, risk management has displaced cost-efficiency as the top drivers of network changes.
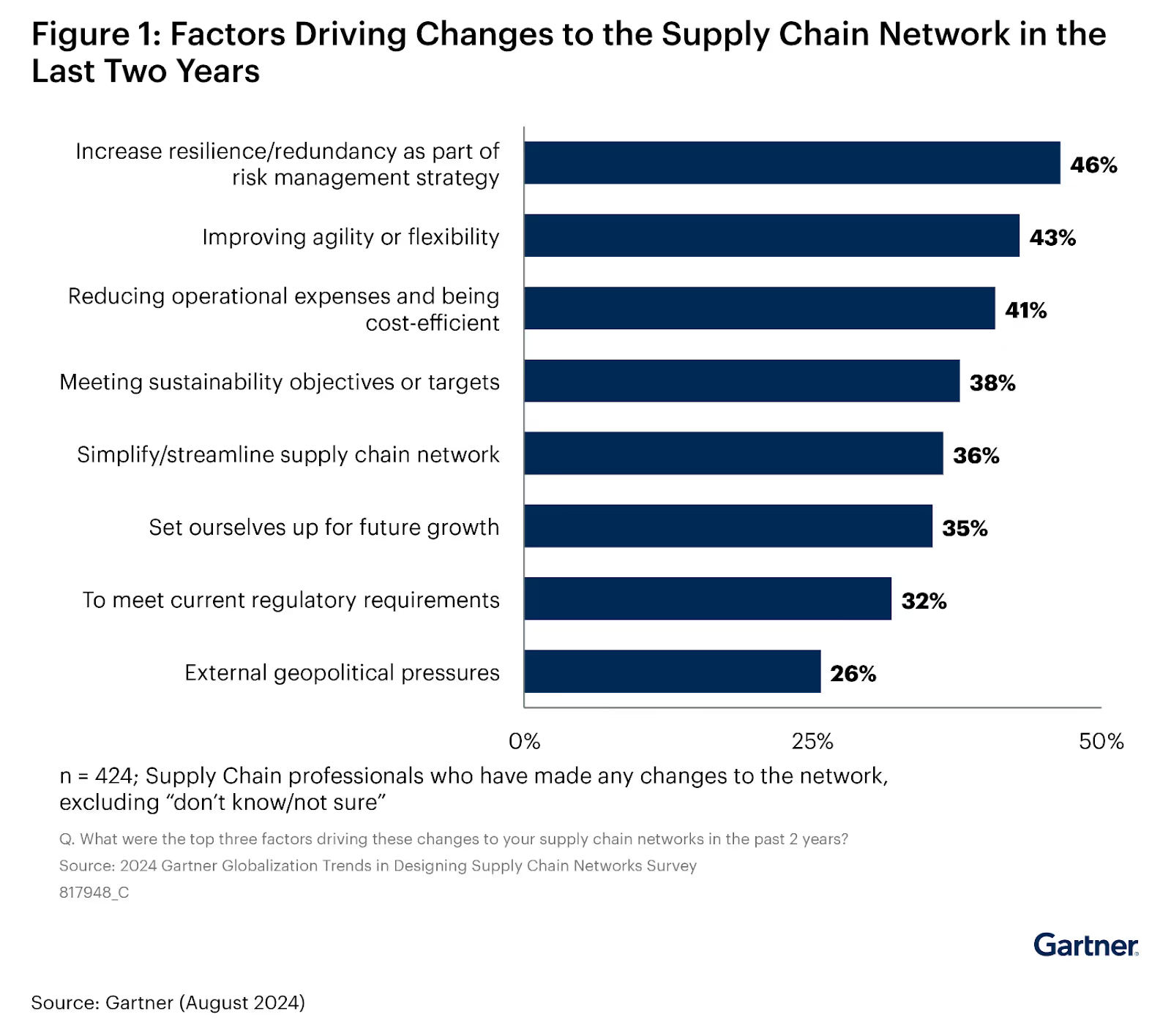
Warehouse management also plays a critical role in driving key performance indicators (KPIs). According to the Association for Supply Chain Management, some of the most important KPIs to track include:
- Fulfillment metrics: Companies want to track order fill rate, fulfillment time, picks per hour, and on-time in full (OTIF) to ensure timely and complete order delivery.
- Inventory accuracy: inventory accuracy involves regular checks against database records and cycle counts to reduce errors and avoid unexpected stockouts.
- Throughput: Throughput measures the daily processing rate of orders to gauge warehouse efficiency.
- Replenishment efficiency: Companies want to monitor stock movement from reserve to primary storage, aiming to avoid shortages or overstock.
- Order accuracy: It’s important to ensure high accuracy (99.5%+) in fulfilling orders to meet customer expectations.
- Inventory turnover: Inventory turnover tracks how quickly stock is received, processed, and delivered to maintain optimal inventory levels.
- Dead stock: Tracking dead stock identifies and addresses slow-moving or unsellable inventory to free up space and reduce waste.
- Supplier reliability: Companies want to measure supplier performance in areas like reliability, compliance, and cost-efficiency for improved procurement.
What Is a Warehouse Management System?
A warehouse management system (WMS) is a comprehensive software solution designed to optimize various warehouse operations, from when goods enter a facility to when they leave. The WMS is meant for warehouse managers but they can be integrated with enterprise resource planning (ERP) systems, customer relationship management (CRM) systems, transportation management systems (TMS), and inventory management systems. By automating tasks such as data entry and inventory tracking, a WMS enhances operational accuracy and efficiency while reducing the risk of human error.
The WMS market is rapidly growing. The U.S. warehouse management system market size was valued at $783.0 million in 2023 and is projected to grow at a CAGR of 20.0% from 2024 to 2030. This growth reflects the increasing need for businesses to streamline warehouse operations in a competitive logistics landscape.
Key Benefits of Using a WMS
Implementing a WMS offers numerous advantages for businesses looking to streamline their warehouse operations.
Improved inventory accuracy and control
A WMS provides real-time tracking of inventory, significantly improving accuracy. With automated data entry and live updates, companies can minimize stock discrepancies and ensure that the right products are always available. A study by Deloitte found that an improvement of 500 basis points in forecast accuracy can result in a reduction of up to four days in finished goods inventory for consumer products companies.
Enhanced order fulfillment efficiency and accuracy
A WMS optimizes the picking process by organizing efficient picking routes and reducing errors. Today, retailers are packing e-commerce orders at their stores as well as warehouses to speed deliveries and tap into more inventory.
Reduced labor costs
Automating warehouse operations through a WMS leads to more streamlined workflows, fewer manual tasks, better labor utilization, and significant cost reductions. This efficiency allows companies to manage growing order volumes without increasing expenses.
According to the Wall Street Journal, only about 20% of warehouses used automation systems in 2022, but companies that invest in automation see significant cost savings. Apo.com Group’s 220,000-square-foot automated warehouse handles up to 30,000 orders daily with only about 20 workers per shift, compared to the 400 employees a manual warehouse setup would require.
Improved warehouse space utilization
A WMS helps optimize storage space by organizing inventory in the most efficient way possible. Through advanced slotting techniques, companies can increase their warehouse space utilization, allowing them to store more products without requiring additional storage facilities. In fact, companies are using three-dimensional robotic warehouse systems to store the same amount of goods in a fraction of the floor space.
Real-time visibility into warehouse operations
With a WMS, warehouse managers gain real-time visibility into critical aspects of their operations, such as inventory levels, order status, and shipping progress. As orders come in, the WMS provides real-time updates on stock levels, allowing managers to quickly identify which items are running low and need restocking.
Real-time visibility is great for tracking inventory of seasonal products. According to NRF forecasts for 2024, holiday spending will reach record levels during November and December and will grow between 2.5% and 3.5% over 2023 to between $979.5 billion and $989 billion.
Scalability to accommodate business growth
A modern, scalable WMS allows businesses to expand operations seamlessly as demand increases. It allows businesses to handle higher volumes of orders and inventory without a complete system overhaul. For example, as a business expands their product range and order volume, they can easily upgrade their WMS to incorporate automation across picking, packing, and shipping and real-time analytics.
Implementing a WMS offers a variety of benefits to businesses. Warehouse operations can become more accurate, efficient, cost effective, scalable, and more. With these advantages in mind, let’s explore the six essential warehouse management processes that form the backbone of effective warehouse management.
6 Core Warehouse Management Processes
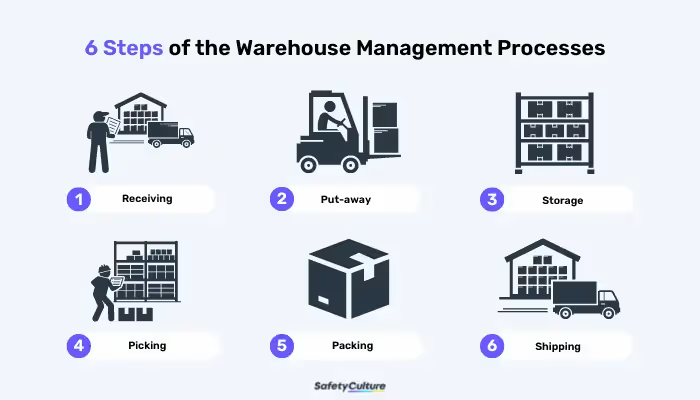
The 6 core warehouse management processes are receiving, put-away, storage, picking, packing, and shipping.
1. Receiving
The receiving process is the foundation of warehouse management. Warehouse receiving encompasses all inbound processes to receive, record, and store incoming inventory and shipments in a warehouse or fulfillment center. Key tasks include unloading and inspecting shipments, verifying inventory counts, managing documentation, and organizing products within the facility.
The goal of effective receiving is to accurately account for and efficiently store goods, ensuring they’re ready for subsequent operations like picking, packing, and shipping.
2. Put-away
The putaway process involves systematically moving items from a received shipment to designated storage locations, ensuring optimal organization and easy access. This method takes into account factors such as space availability, warehouse size, and specific item requirements like weight, variety, and storage conditions.
A warehouse manager coordinates stock checks, places replenishment orders, and, when inventory arrives, works with staff to unload and organize items using equipment like forklifts. Putaway strategies, such as slotting or ABC analysis, are selected based on the company’s specific needs. Below is an illustration of various put away strategies.
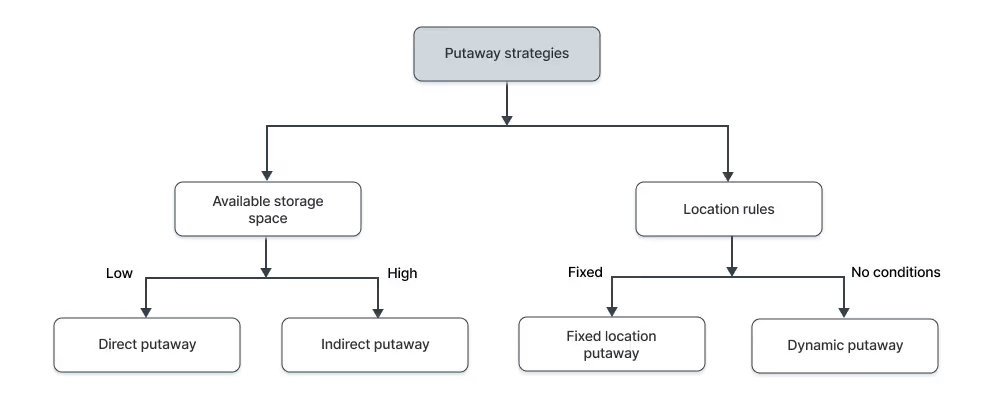
3. Storage
The cost of warehouse space is rising. In 2023, U.S. warehouse and distribution space rental rates surged to a record-breaking $9.72 per square foot, marking a 20.6% increase from the previous year, according to a Colliers report. For warehouse operators, it’s critical to optimize warehouse storage in order to maximize available space and enhance efficiency.
Strategies include organizing items based on demand, size, and picking frequency. Techniques like slotting and vertical storage improve accessibility and reduce travel time, helping warehouses handle higher volumes with lower costs.
4. Picking
Picking is one of the most labor-intensive tasks in warehouse management, where items are selected to fulfill customer orders. The process can be optimized using different methods, such as single-order picking or batch picking. Efficient picking strategies, such as zone picking and wave picking, are tailored to different warehouse layouts and order profiles. Picking strategies can reduce the time spent traveling between areas, streamlining the overall order fulfillment process and enhancing speed and accuracy.
Not all picking strategies have to involve technologies. Optimizing facility layouts can have a large impact as well. For example, according to research by McKinsey, a pharma warehouse was able to reduce process time by 20% simply by eliminating picking from the highest shelves.
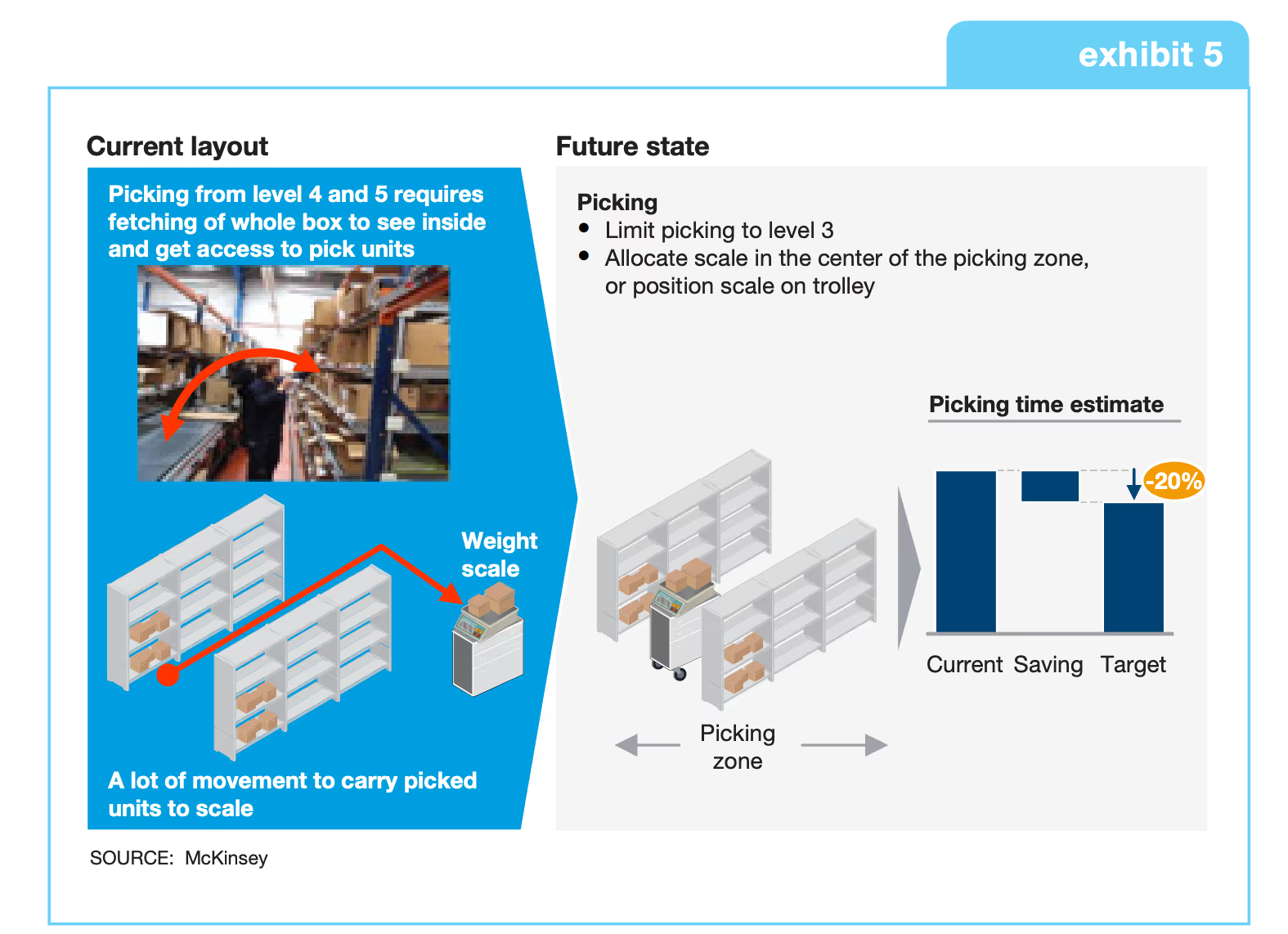
5. Packing
The packing process ensures that items are securely prepared for shipping. This step is vital for protecting products from damage during transit. Using the right packing materials can reduce shipping damage, minimizing returns, and enhancing customer satisfaction. Proper packing is key to ensuring that items reach their destination in perfect condition. Some important strategies include cartonization, kitting, and branded packaging.
A great example to follow is Amazon. The e-commerce giant utilizes lighter, more flexible, and right-sized packaging to reduce delivery emissions per package by using less material and taking up less space in delivery vehicles. They’ve reduced the average per-shipment packaging weight by 43% and avoided more than 3 million metric tons of packaging, including more than 446,000 metric tons in 2023 alone.
6. Shipping
Shipping includes routing orders, selecting carriers, and preparing shipment documentation. Efficient shipping is critical for maintaining customer satisfaction through timely deliveries. Shipping is a crucial step in warehouse management processes, involving order routing, carrier coordination, shipment documentation preparation to ensure timely deliveries. Integrating a Warehouse Management System (WMS) with shipping carriers streamlines this process by providing real-time shipment tracking and improving communication, which optimizes delivery schedules.
According to PwC, 50% of supply chain cost savings can be attributed to smart logistics. This involves connecting warehouses with other parts of the supply chain and automating functions like labor management, inventory visibility, and storage and handling. However, while 65% of “digital champions” have implemented integrated warehouse management capabilities, only 36% of all companies have them.
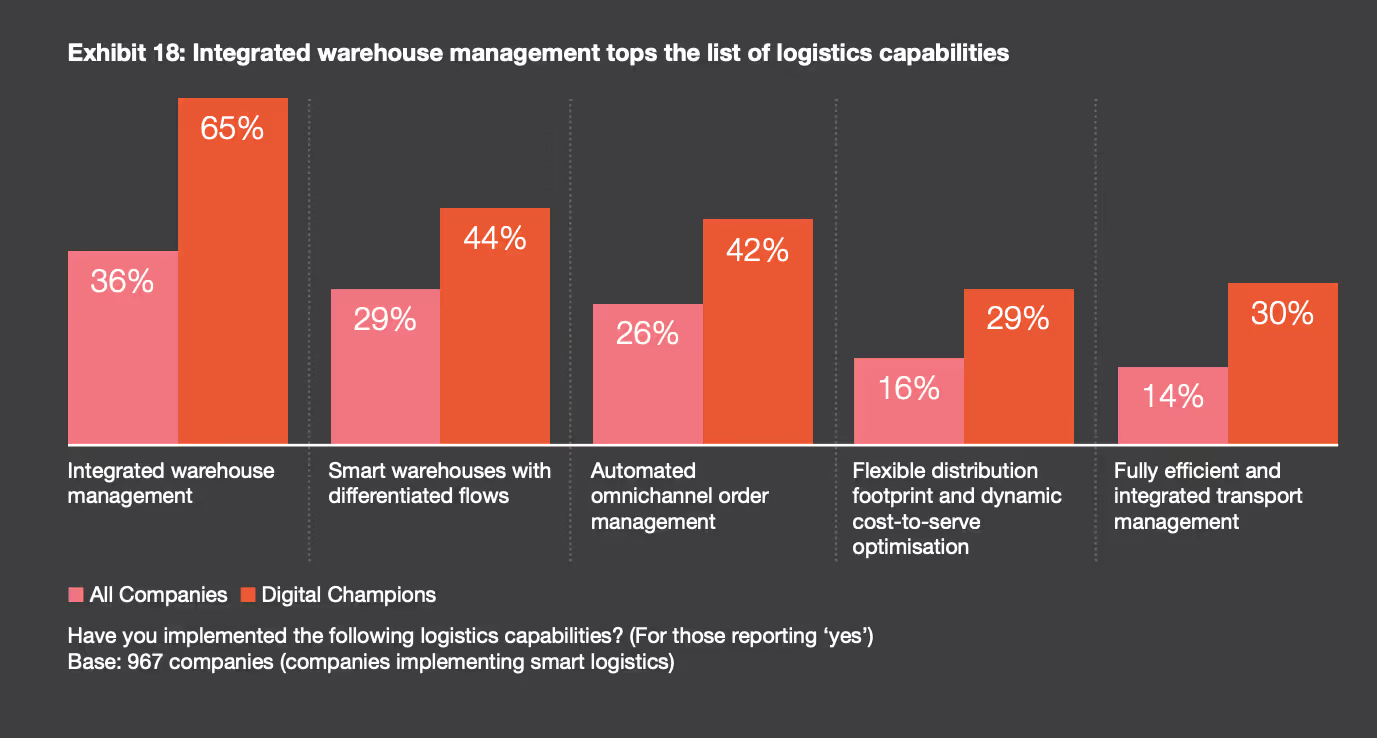
Receiving, put-away, storage, picking, packing, and shipping form the foundation of efficient warehouse operations. Each process ensures that the flow of goods is optimized so that products can get in the hands of customers faster and more accurately. To enhance these processes further, businesses can adopt tech-powered strategies that can boost operations.
Top 5 Tech-Powered Strategies to Improve Warehouse Management
Technology today plays an increasingly critical role in creating connected and autonomous supply chain ecosystems. In warehouses, where many manual and inefficient processes still exist, there are exciting opportunities to leverage modern tech solutions to enhance overall operations. Here are the top five tech-powered strategies to improve warehouse management:
1. Implement a WMS
A WMS paired with inventory management software is crucial for optimizing warehouse operations. This integration centralizes inventory data, providing real-time visibility into stock levels, orders, and shipments. It allows businesses to efficiently monitor and control inventory, streamlining processes like receiving, putaway, and storage.
For instance, PackageX offers a modern WMS that connects your warehouse activity to your receiving, inventory, and fulfillment operations to support fast-moving logistics. It automates inventory verification and data entry, which streamlines the receiving process, minimizes errors, and enhances overall operational efficiency.
2. Use data analytics for demand forecasting
Leveraging data analytics allows businesses to analyze historical sales data, seasonal trends, and market dynamics to better synchronize inventory levels with actual demand. This strategic approach minimizes the risk of stockouts and overstock, making inventories leaner and tying up less working capital. For example, a retailer might use analytics tools to predict high demand during holiday seasons, ensuring they stock sufficient inventory to meet customer demand.
3. Invest in automation and robotics
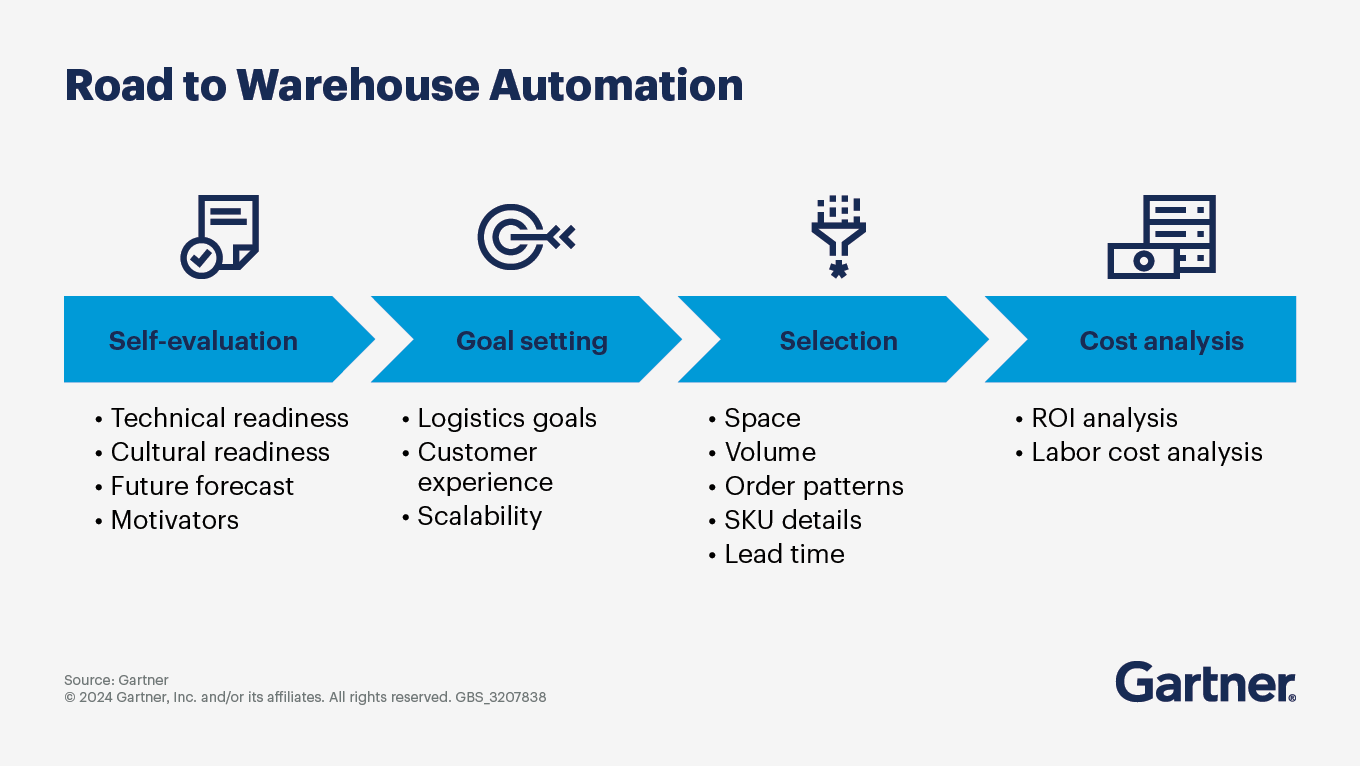
Gartner defines warehouse automation as the use of hardware, software and other technology solutions to streamline supply chain and warehouse operations. Incorporating automation and robotics into warehouse operations significantly reduces labor-intensive tasks and improves accuracy. It can involve robots picking inventory and packaging items for shipment, conveyor systems transporting products throughout a warehouse, software helping with warehouse management and other tools reducing the reliance on human labor.
The road to warehouse automation involves self evaluation, goal setting, selection, and cost analysis. Companies like Amazon have successfully implemented robotics to streamline their warehouse operations, resulting in faster order fulfillment and reduced operational costs.
4. Integrate IoT devices for real-time monitoring
The Internet of Things (IoT) enables real-time tracking of inventory and environmental conditions in warehouses, allowing for proactive adjustments and predictive maintenance. For example, a warehouse equipped with IoT sensors can monitor temperature and humidity levels for sensitive products, ensuring optimal storage conditions.
Connectivity ensures reliable data transmission through various technologies, while robust data processing capabilities provide actionable insights, and user interfaces facilitate easy access to this information. IoT not only improves inventory management but also enhances product quality and reduces spoilage.
5. Adopt smart warehouse technologies
Smart warehouses leverage cutting-edge technologies to streamline operations and maximize efficiency. Adopting smart warehousing technologies transforms operations and maximizes efficiency by integrating advanced systems.
Technologies like Radio Frequency Identification (RFID) facilitate contactless inventory tracking, while the Internet of Things (IoT) enables seamless data exchange between devices and warehouse systems. Robotics, including autonomous and collaborative robots, optimize workflows, and Automated Guided Vehicles (AGVs) transport goods independently. Coupled with Optical Character Recognition (OCR), QR codes, and barcodes, these tools enhance accuracy during the receiving process by automating data extraction and minimizing errors.
For instance, PackageX utilizes advanced label and BOL scanning technologies to achieve 95% scan accuracy, making its software the most accurate in the market.
Supercharge Your Warehouse Operations With PackageX
Whether it’s coordinating fulfillment, ensuring accurate inventory levels, or streamlining picking, packing, and shipping processes, optimizing warehouse management helps to minimize disruptions and enhance customer satisfaction. Leveraging advanced tech to automate warehouse processes can significantly bolster a company’s supply chain.
PackageX empowers businesses to digitize their operations through a comprehensive suite of integrated applications and APIs. Our unified platform offers powerful warehouse and inventory management solutions and AI-driven scanning capabilities that enhance efficiency in warehouse workflows.
To discover how PackageX can optimize your warehouse operations, reach out to our team or schedule a demo to see our platform in action.
FAQ
What does warehouse management do?
Warehouse management oversees the efficient operation of storage and distribution processes, including inventory control, order fulfillment, and shipping. It aims to optimize workflows, reduce costs, and improve customer satisfaction.
What are the 6 essential warehouse management processes?
The 6 core warehouse management processes are receiving, putaway, storage, picking, packing, and shipping.
What is the best way to manage a warehouse?
The best way to manage a warehouse involves implementing a robust warehouse management system (WMS), optimizing layout for efficiency, training staff, implementing best practices, and utilizing tech-powered strategies like smart warehouses, IoT, automation, robotics, and data analytics.
What is the most important thing in warehouse management?
The most important aspect of warehouse management is maintaining accurate inventory levels to ensure timely order fulfillment while minimizing costs associated with overstocking or stockouts. This includes processing sales orders quickly, organizing material handling and storage efficiently, processing transactions promptly, and linking warehouse management directly to sales order processing for seamless operations. Keeping optimal stock levels and enhancing overall efficiency are crucial for success in warehouse management.