Picture a busy warehouse where packages arrive daily, each accompanied by hordes of paperwork, including shipping labels, invoices, and packing slips.
Workers spend valuable hours manually entering data from these documents into a system—a laborious process prone to errors.
Now, imagine a more efficient scenario: a simple scan that empowers workers to capture all information from those documents in seconds without manual entry, saving them valuable time and effort.
This is just one example of the power of OCR document scanning software. But what is OCR? Why should you even care? And how can you use it in the supply chain?
What is OCR?
Optical character recognition (OCR), also known as text recognition, is a technology that converts images of typed, handwritten, or printed text into an editable and searchable format on a computer. A common example is digitizing a paper receipt into an editable digital format.
In the context of the supply chain, OCR offers significant benefits.
OCR, Data Extraction, and Traceability in the Supply Chain
OCR eliminates the need for manual data capture by converting text from paper documents, such as invoices and receipts, into digital characters.
It also accelerates the processing of crucial documents like shipping labels and packing slips, ensuring that information is swiftly captured and integrated into your inventory management system (IMS) for real-time tracking. This not only helps maintain accurate and up-to-date records but also enhances supply chain visibility and traceability, thereby improving decision-making with reliable data.
Lastly, OCR enables seamless data integration across systems, ensuring a smooth flow of information from procurement to delivery. For example, OCR can automatically integrate digitized invoices into your ERP system for consistency and financial accuracy.
Diving deeper, OCR offers plenty of use cases across warehouses, stores, and last-mile operations.
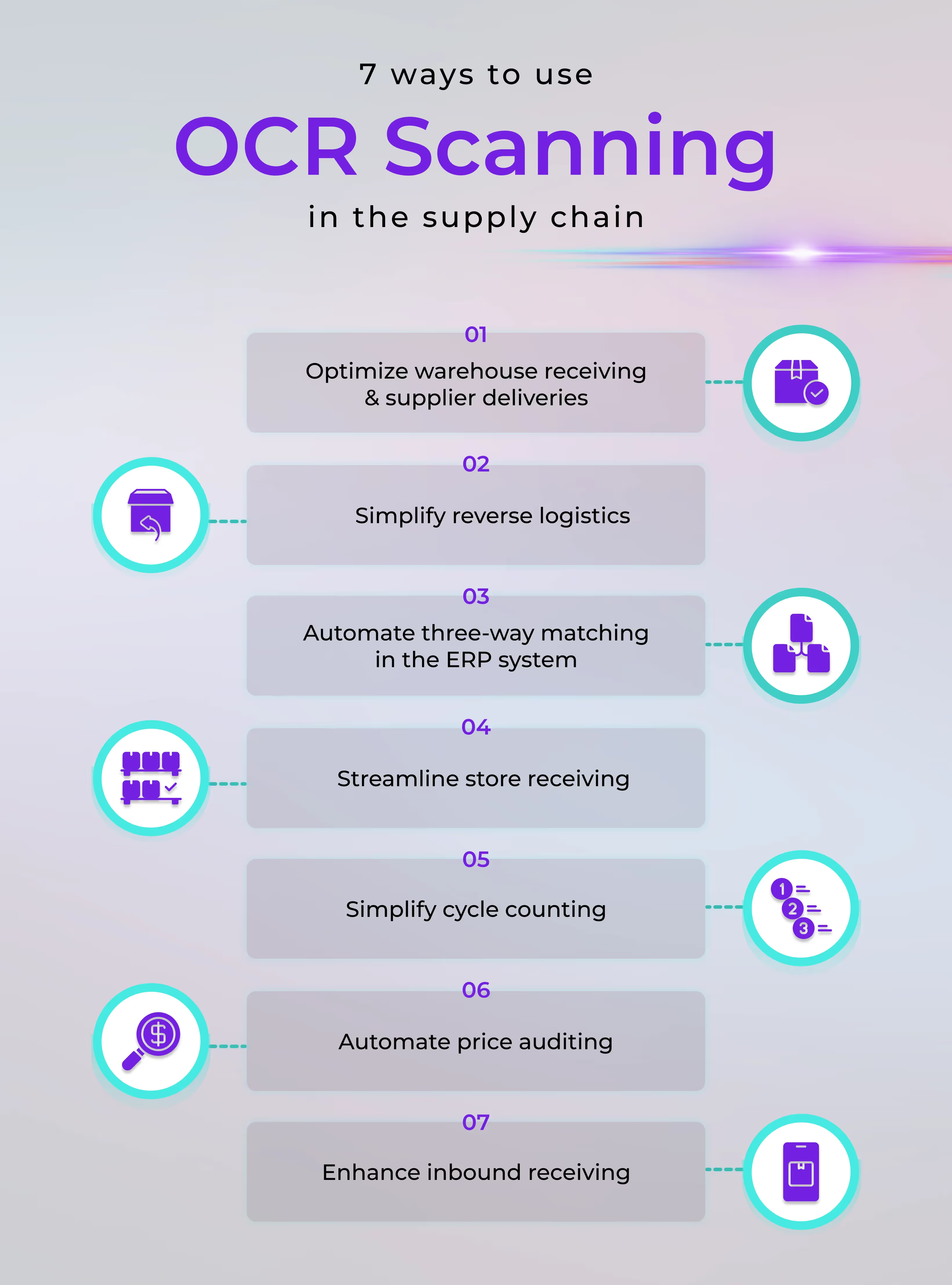
At the Warehouse
Warehouse processes involve multiple steps, such as receiving, storing, packing, and shipping. However, a lack of digitization and automation often hamper these steps.
This generates a lot of paperwork and causes numerous bottlenecks, such as manually verifying received goods against purchase orders. In short, the absence of automation leads to warehouse inefficiencies.
While barcode scanning software can help by automating some of the data capture and reducing processing time, it’s limited to barcodes and cannot encode extensive information. If a barcode is missing or unreadable, barcode scanning becomes ineffective.
In contrast, OCR is a more versatile tool that addresses many of these concerns across critical processes, giving you the flexibility to adapt to various scenarios.
1. Optimize Warehouse Receiving & Supplier Deliveries
Warehouse receiving includes all operations related to accepting, recording, and storing incoming packages and shipments from suppliers.
When receiving and unloading products, staff can use OCR scanners to capture text directly from documents, speeding up the receiving process and ensuring data accuracy. Documents include bills of lading and shipping manifests, and captured text could potentially include shipment details, serial numbers, and SKU numbers.
Staff can also track detailed information throughout the receiving process using OCR-equipped smartphones. These devices use QR codes, barcodes, and RFID technologies to extract data.
OCR technology enables smartphones to function as universal label scanners, capable of scanning in low-light conditions and reading damaged labels.
2. Simplify Reverse Logistics
Reverse logistics involves transporting goods from their final destination back to the manufacturer or supplier for recycling, repairs, warranty claims, or returns.
With OCR technology, staff can scan and process return labels, allowing for easy integration into digital returns portals, WMS and Inventory System. This streamlines the return process and helps you quickly log returned products into inventory and the system with minimal delays.
3. Automate Three-way matching in the ERP system
Three-way matching involves comparing three key documents—purchase orders, invoices, and receiving documents—to identify discrepancies and ensure accuracy.
OCR captures data from these documents and uploads it to the ERP system for processing. Once uploaded, the system performs real-time validation and reconciliation, promptly resolving discrepancies and ensuring accurate information across documents.
At Your Store
The store receiving process usually involves accepting deliveries, verifying received stock, and updating inventory systems. Once done, cycle counting and price auditing are often undertaken to maintain inventory accuracy and price integrity.
During these processes, OCR can enhance efficiency.
4. Streamline Store Receiving
When a package arrives, an employee traditionally verifies it against the purchase order or packing slip to confirm the correct product and quantities. They then enter SKU numbers and unit prices into an IMS.
While store receiving is generally less complex than warehouse receiving, focused primarily on managing incoming goods for direct sale to consumers, it can still benefit from OCR.
Without manual entry, staff can use an OCR scanner to pull essential information from delivery labels, including product details, quantities, and prices. This reduces recording errors and speeds up the process of updating inventory systems.
5. Simplify Cycle Counting
Cycle counting is a routine inventory auditing procedure where a subset of inventory is counted at regular intervals. Traditionally conducted via physical counts or barcode scanners, more retailers are now adopting OCR.
OCR streamlines data capture, eliminating the need for physical counts and, unlike barcode scanners, reads text even if barcodes are damaged or missing.
6. Automate Price Auditing
Price auditing involves verifying that item prices on shelves match those stored in the inventory management system (IMS).
OCR document scanning integrates with your IMS for efficient price auditing. Employees scan shelf labels to pull data like product names and prices. The system checks price accuracy automatically, requiring no manual verification.
At a Building or Campus
Inbound receiving at buildings or campuses, especially in last-mile operations, involves managing the final delivery stages before products reach their ultimate destination. Incoming shipments are verified, inventory systems updated, and packages sorted before final delivery.
This final stage can be particularly challenging due to the high volume of packages handled.
Any flaws in your current inbound receiving process are quickly exposed and often compounded. Inaccurate inbound receiving technology only intensifies delays. If a barcode scanner struggles with a damaged barcode, this issue may become more frequent with increasing volume.
A lack of automation also causes greater inefficiencies and inaccuracies at scale. Physically handling and verifying each package and inputting data into a system becomes increasingly time-consuming as package volume rises, leading to significant processing delays. Errors inherent in manual processing also become more likely with increased volume.
Lastly, an inadequate package tracking process at scale complicates item location and increases the risk of lost packages. Barcode scanning, for instance, often lacks detailed information about a package’s delivery location.
However, OCR barcode scanning software can, once again, address these challenges.
7. Enhance Inbound Receiving
With OCR able to read text from documents and packages even if barcodes are defective, you can easily capture package information when things get busy. Some QCR software even uses AI to combine QR, text, and barcodes to collect all information on the label and can turn your smartphone into a mobile scanner.
As demonstrated earlier, automated data capturing also minimizes physical handling and input, which accelerates package verification, helps maintain accuracy at scale, and automatically outlines the next steps in processing. Some OCR solutions can reduce package processing times to just a few seconds.
Furthermore, OCR enhances visibility and traceability by directly extracting crucial information from scanned documents and integrating it into tracking systems for real-time package monitoring across the supply chain. This includes package identification numbers, recipient addresses, and delivery statuses.
The result? Instances of lost packages are significantly reduced.
{{returns-webinar}}
Modernize delivery management with the right tech partner
OCR document scanning software transforms the supply chain by automating data capture, reducing errors, and enhancing visibility and traceability. The seven OCR use cases highlighted showcase its versatility, from simplifying reverse logistics in your warehouse to automating price auditing at your store to enhancing inbound receiving at your building.
The key lies in partnering with the right technology partner. PackageX is at the forefront of modernizing delivery management with an end-to-end solution for receiving, storing, routing, and delivery.
PackageX offers AI-trained scanning technology for comprehensive data capture via QR, text, and barcode recognition and provides lightning-fast response time with 95% accuracy.
You also gain access to a user-friendly interface that requires minimal training and the option to integrate PackageX into your existing tech stack or use it as a standalone solution.
Request a demo today and discover more about our end-to-end solution, which is helping hundreds of B2B and Fortune 100 companies exceed their customer expectations by digitizing and connecting inventory, fulfillment, shipping, and receiving on one platform.